*On June 1, 2023 Emerson’s Climate Technologies business became a new standalone company – Copeland. Though our name has changed, we are building on more than a century of HVACR innovation and industry leadership, and Copeland continues to offer the same products, industry stewardship, and learning opportunities you’ve grown to trust. Information found on this webpage posted before June 1, 2023 may contain our old name or branding, but you can be at ease knowing it was created with the knowledge and expertise of Copeland.
Welcome to the fourth installment in our series of blogs intended to help not just beginning service technicians, but anyone who wants to learn more about the basics of refrigeration. In this blog, I explain the nuances of vapor injection along with the full refrigeration cycle. For this blog series, we have also created companion videos about each topic that you can cross-reference while accessing related information at Education.Emerson.com.
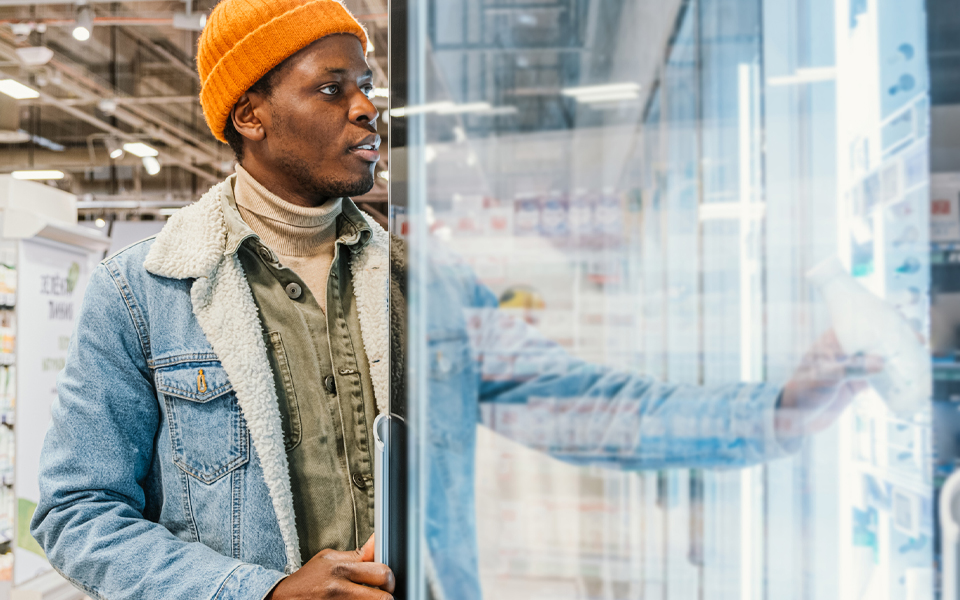
Comparing Refrigeration to a Baseball Diamond
The refrigeration cycle requires four main components. No matter how small or how large a cooling system might be, its design will include a compressor, a condenser, a metering device and an evaporator.
When I teach new technicians, I often compare the refrigeration cycle to the layout of the field for the game of baseball. I’ve found this analogy makes refrigeration equipment and processes easier for them to understand.

In my example, a compressor is located at home plate at the bottom of the baseball diamond (shown above). In a refrigeration or cooling system, compression is the first step:
-
- Refrigerant enters as a low-pressure (LP), low-temperature (LT) superheated vapor and exits the compressor as a high-pressure (HP), high-temperature (HT) vapor.
- The compressor mechanically compresses the refrigerant gas.
- Under pressure, the refrigerant volume is reduced and the temperature is raised.
The second step involves a condenser, located at first base on the right side of the baseball diamond:
-
- Hot, pressurized refrigerant gas arrives from the compressor into the condenser, which is designed to reject heat by lowering or returning the temperature of the refrigerant to its condensing temperature.
- As it rejects heat, the condenser converts the vapor to a sub-cooled liquid.
- In most condensers, the refrigerant gas enters at the top of the equipment and leaves at the bottom because the refrigerant in a liquid state is much heavier than the weight of refrigerant in a gas state.
In the third step, a metering device located at second base at the top of the baseball diamond regulates the amount of refrigerant released into the evaporator in response to the cooling load and causes a pressure drop.
The metering device also:
-
- Measures the superheat at the evaporator outlet
- Maintains a constant temperature by raising or lowering the amount of refrigerant flowing into the evaporator
At the fourth step, cold liquid refrigerant mixes with vapor causing the saturation temperature as it boils off or vaporizes in the evaporator, located at third base, on the left side of the baseball diamond:
-
- The process allows the refrigerant to absorb heat through a series of metal coils.
- The low-pressure superheated vapor refrigerant gas then returns to the compressor to continue the refrigeration process.
Here is the value of comparing the refrigeration process to a baseball diamond: If I draw a vertical line from home plate up to second base, everything in the system on the right side of that line is under high pressure; everything on the left side of that line is low pressure.
Likewise, if I draw a horizontal line from first base to third base, the refrigerant above the line is in a liquid state; below the line, the refrigerant is a vapor, regardless of whether it is under high or low pressure.
Liquid Injection Cools Compressor and Increases Capacity
A compressor is designed to operate at very high temperatures, so a liquid injection method has been developed to cool the compressor internally. How this works can be confusing; refrigerant is injected in a vapor state, not in a liquid state.
When necessary, liquid injection cools a compressor to enable it to run reliably under difficult high compression ratio conditions normally seen on low-temperature freezer applications.
-
- Refrigerant is piped from the system liquid line, through an injector valve to the compressor; in scroll compressors, the refrigerant is injected directly into the scroll elements.
- Without this cooling, the compression elements can get too hot and the oil breaks down, leading to compressor failures.
Another approach called enhanced vapor injection (EVI) increases refrigeration capacity and, in turn, the efficiency of the system:
-
- A heat exchanger is utilized to provide subcooling to the refrigerant before it enters the evaporator.
- A small amount of refrigerant is evaporated and superheated above its boiling point.
- This superheated refrigerant is then injected mid-cycle into the scroll compressor and compressed to discharge pressure.
The diagram below shows how enhanced vapor injection (EVI) increases the efficiency of the system.

EVI increases the compression ratio and, in the process, boosts capacity for the refrigeration system. The greatest gains can be achieved during the summer months and other periods when warm ambient temperatures require more cooling.
View our new video series to learn more about the refrigeration cycle. For a deeper dive into all of our training content and access to our other educational resources, visit Education.Emerson.com.
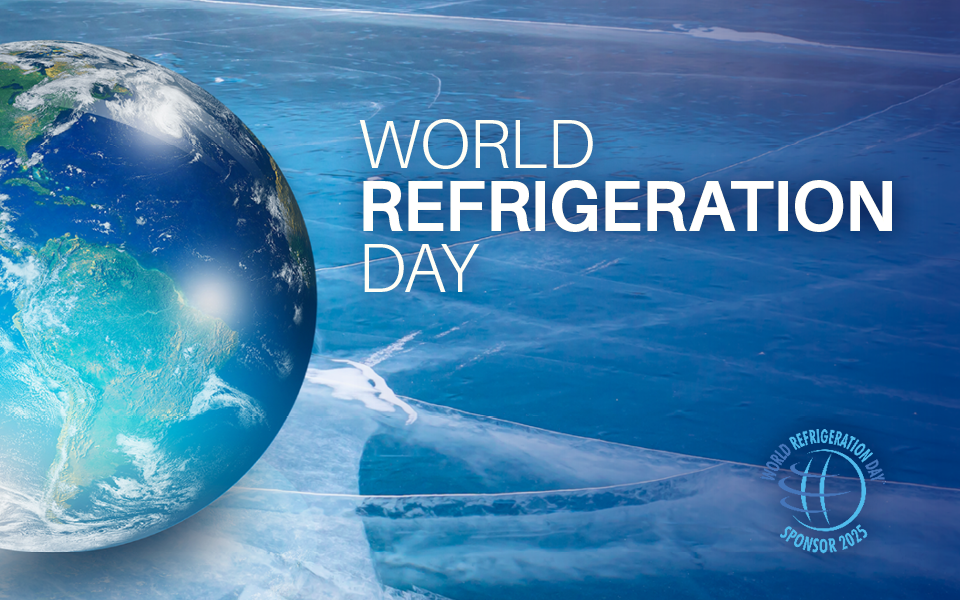
Celebrating World Refrigeration Day 2025
Electrical component considerations for A2L system safety Heating, ventilation, air conditioning...
A2L Refrigeration Overview — Systems, Safety and Servicing Considerations
*On June 1, 2023 Emerson’s Climate Technologies business became a new standalone company –...
Servicing the Next Generation of Lower-GWP Refrigerants
*On June 1, 2023 Emerson’s Climate Technologies business became a new standalone company –...