*On June 1, 2023 Emerson’s Climate Technologies business became a new standalone company – Copeland. Though our name has changed, we are building on more than a century of HVACR innovation and industry leadership, and Copeland continues to offer the same products, industry stewardship, and learning opportunities you’ve grown to trust. Information found on this webpage posted before June 1, 2023 may contain our old name or branding, but you can be at ease knowing it was created with the knowledge and expertise of Copeland.
As recent regulations set the stage for the use of A2L refrigerants in HVACR, commercial refrigeration stakeholders have questions about system design, safety considerations and servicing best practices. Whether you’re an original equipment manufacturer (OEMs), system designer or service technician, working with lower-flammability A2Ls will require familiarity with standards and procedures that ensure system safety. In a recent article for RSES Journal, I provided an overview of the A2L equipment landscape and discussed how it impacts system design and servicing.
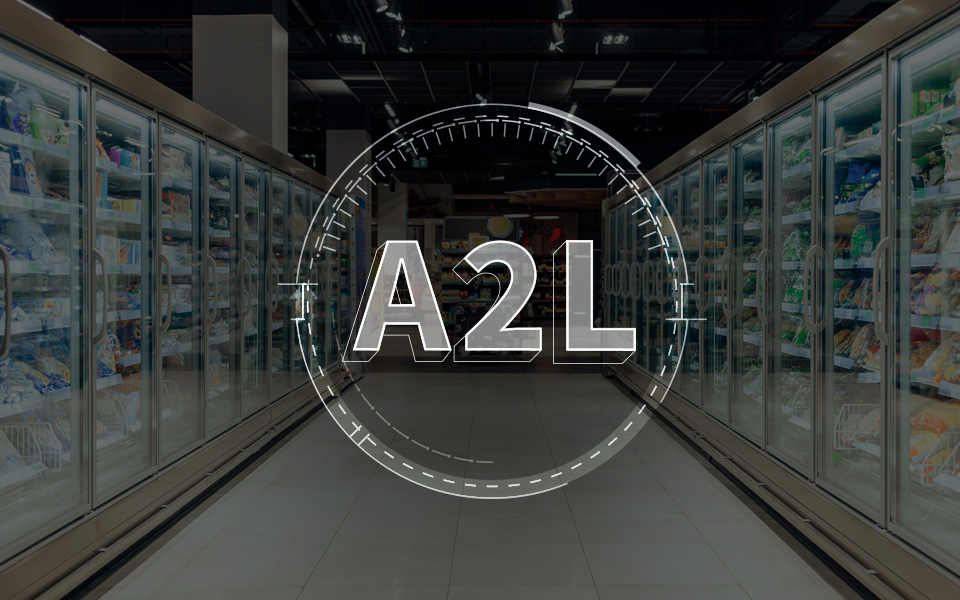
What does the A2L classification mean?
ASHRAE has classified A2L refrigerants with a lower-flammability rating. Compared to the higher-flammability A3 R-290 (aka propane) — which has been used in small-charge, stand-alone units for more than a decade — A2Ls have lower-flammability characteristics across all key metrics. From a regulatory compliance perspective, A2Ls offer lower-global warming potential (GWP) ratings below the 150 and 300 thresholds.
Lower flammability limit (LFL) — The LFL of A2Ls designed for commercial refrigeration is roughly eight to 10 times higher than R-290. The Underwriters Laboratories (UL) 60335-2-89, 2nd edition safety standard has approved the use of A2Ls in significantly larger charges, which can potentially support much higher-capacity applications. Because A2Ls are composed of different blends, the specific LFL rating will vary among different types of A2Ls. LFL is a key factor in determining the allowable refrigerant charge per each equipment type and system design.
Minimum ignition energy (MIE) — A2L MIEs are significantly higher than R-290, which can be ignited by lower energy sources such as a static electrical discharge. A2Ls need more energy to ignite, typically requiring exposure to an open flame or strong electrical energy source.
Burning velocity (Su) — Su denotes the velocity of a flammable event. Even if the LFL and MIE create the conditions necessary for ignition, Su for A2Ls is much lower than R-290. The Su of R-290 is 46 cm/s (i.e., a nearly explosive effect), whereas the Su of A2Ls is less than 5 cm/s.
Which systems will use A2Ls?
UL 60335-2-89, 2nd edition, provides guidelines for the safe use of A2L and A3 refrigerants in commercial refrigeration by specifying requirements for equipment design, construction, and installation. For A2Ls, these requirements are defined for two equipment types: self-contained units and remote systems.
Self-contained units — Is defined as equipment consisting of a completely factory-assembled, factory-charged and factory-tested refrigeration system, in which all refrigerant-containing parts are permanently connected at the factory. Thus, the evaporator, condenser and compressor are all part of a packaged unit, such as reach-in display cases. Any A2L self-contained system charged with more than 150g of refrigerant (the current charge limit for R-290) must follow UL 60335-2-89, 2nd edition’s safe construction guidelines. Charge limit calculations are based on whether the unit has a closed- or open-door (or drawer) design. For example, since R-454C has an LFL of 0.291 kg/m3, the refrigerant charge in an open case would be 8.3 lbs. These higher charge limits would greatly expand the cooling capacities found in current self-contained, R-290 systems.
Remote and/or field-erected systems — Unlike R-290, A2Ls have the potential for use in remote, distributed systems — such as condensing units or mini scroll packs — which would enable a new generation of lower-GWP, higher-capacity solutions for commercial refrigeration stakeholders. Because remote systems are largely assembled, charged and installed in the field, they will require adherence to additional safety requirements and considerations. A2L charge limit calculations in remote and/or field-erected systems are proportionate to the application size and/or cooling requirements. Again, using R-454C as an example, the maximum allowable charge size would be 76.2 kg (166 lbs.) and deliver up to 50–60 hp of cooling.
It’s important to note that A2Ls are not a drop-in replacement in existing systems. All A2L refrigeration systems must be designed, optimized and qualified to use A2L components.
What safety measures are required?
Utilizing larger charges of A2L refrigerants in remote systems may require additional safety mitigation measures, which are based on:
- Specific charge of applications
- LFL of the A2L refrigerant
- Room area of the installation space
- Other relevant application conditions
Remote condensing unit OEMs should follow UL 2-89, 2nd edition guidance, under its Annex 101.DVU and Annex 101.DVG requirements. Depending on the application and/or installation conditions, systems should be designed to detect, isolate and disperse A2L refrigerant leaks via a combination of tools and controls:
- Sensors within cases to detect leaks
- Isolation and/or safety shut-off valves (SSOVs) in the refrigeration system to limit releasable charge
- Electronic controls with A2L logic to perform required actions in the event of a leak — such as shutting off the compressor and/or other components
- Ventilation and/or circulation fans within cases or walk-in units
What are the servicing best practices?
When servicing systems with A2L refrigerants, technicians should follow typical refrigerant management best practices and be aware of some new safety considerations. First, identify which A2L refrigerant is being used by checking for refrigerant labels on the system. Look for red markings on all service fittings and be sure to clearly mark them for the next technician who may service the system.
Next, it’s important to use specific tools that are designed for A2L use, such as gauges, vacuum pumps, and leak detection and refrigerant recovery machines. When servicing or repairing A2L refrigerant-based systems, follow three mandatory steps (which are already considered industry-accepted best practices):
- Purge with nitrogen.
- Evacuate the refrigerant.
- Perform leak and pressure tests.
For more information on A2L refrigerants, system design and servicing best practices, please visit our resource hub.
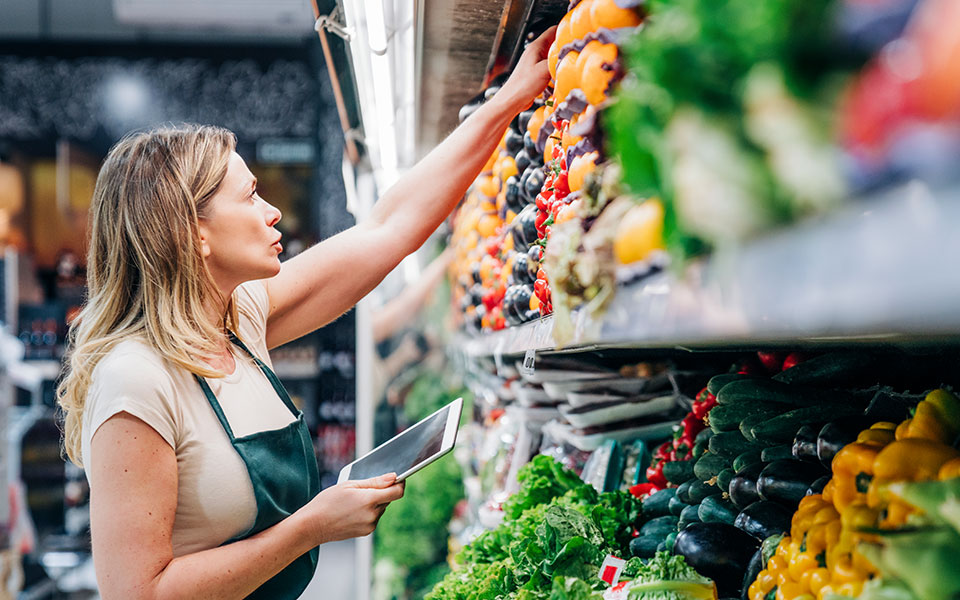
8 proven strategies for rigorous cold chain management
Preparing for the approval and safe use of A2Ls in commercial refrigeration applications...
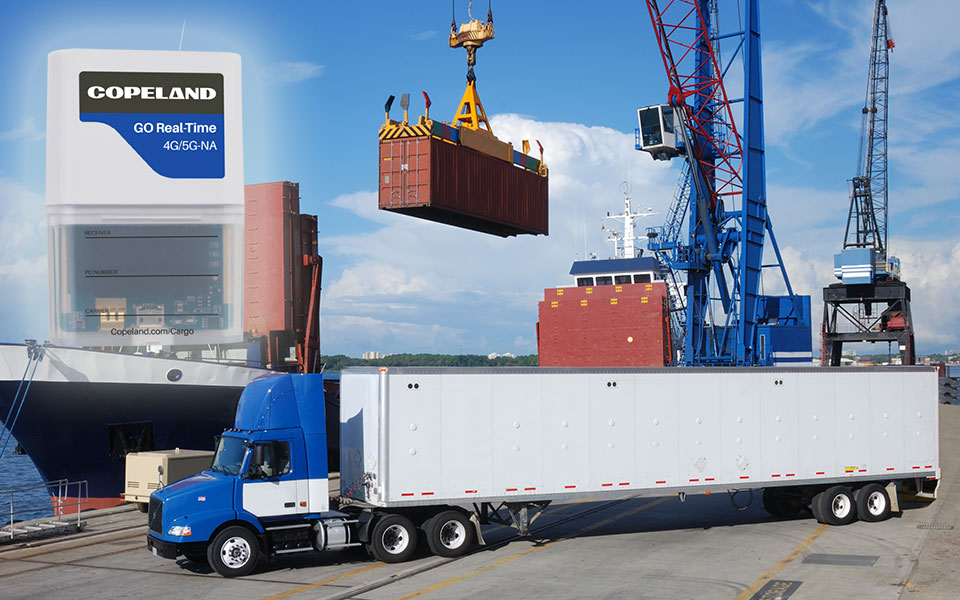
Protection for high-value shipments just got even better
We’re excited to announce the release of Copeland’s newest real-time tracker, the GO Real-Time...
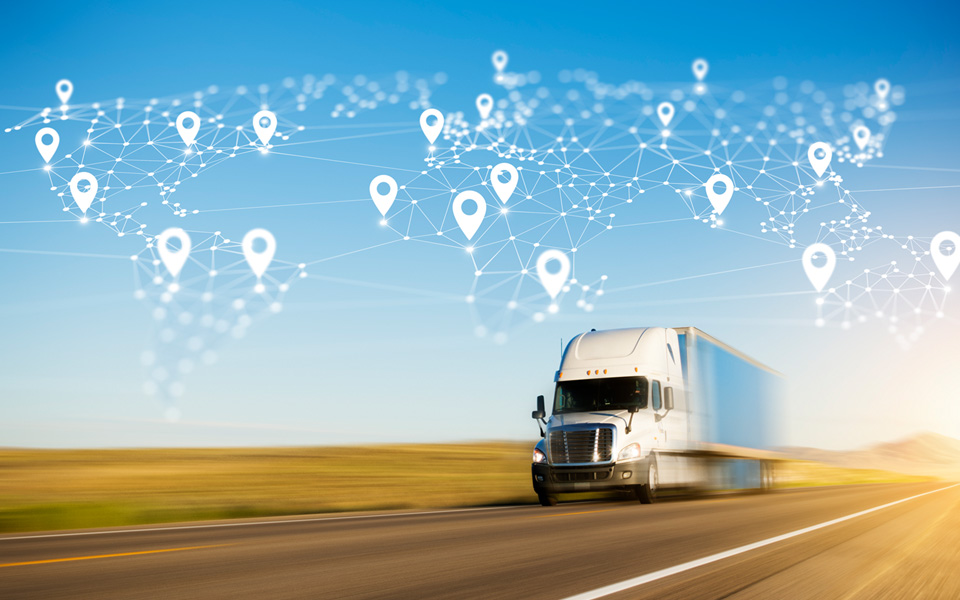
Three proven strategies to prevent cargo theft
The over-the-road (OTR) transport industry is experiencing a surge in cargo thefts. As thieves...