*On June 1, 2023 Emerson’s Climate Technologies business became a new standalone company – Copeland. Though our name has changed, we are building on more than a century of HVACR innovation and industry leadership, and Copeland continues to offer the same products, industry stewardship, and learning opportunities you’ve grown to trust. Information found on this webpage posted before June 1, 2023 may contain our old name or branding, but you can be at ease knowing it was created with the knowledge and expertise of Copeland.
Copeland recently made it a priority to re-think refrigerated case control from the ground up, creating a unit engineered specifically for today’s electronic expansion valve (EEV) equipment. The result is the CC200 case controller designed to handle the unique challenges of retail grocery refrigeration environments. Combined with an all-new Cold Chain Connect app that simplifies setup and commissioning, the CC200 delivers significant improvements in energy savings, reliability, serviceability, food quality and overall store health.
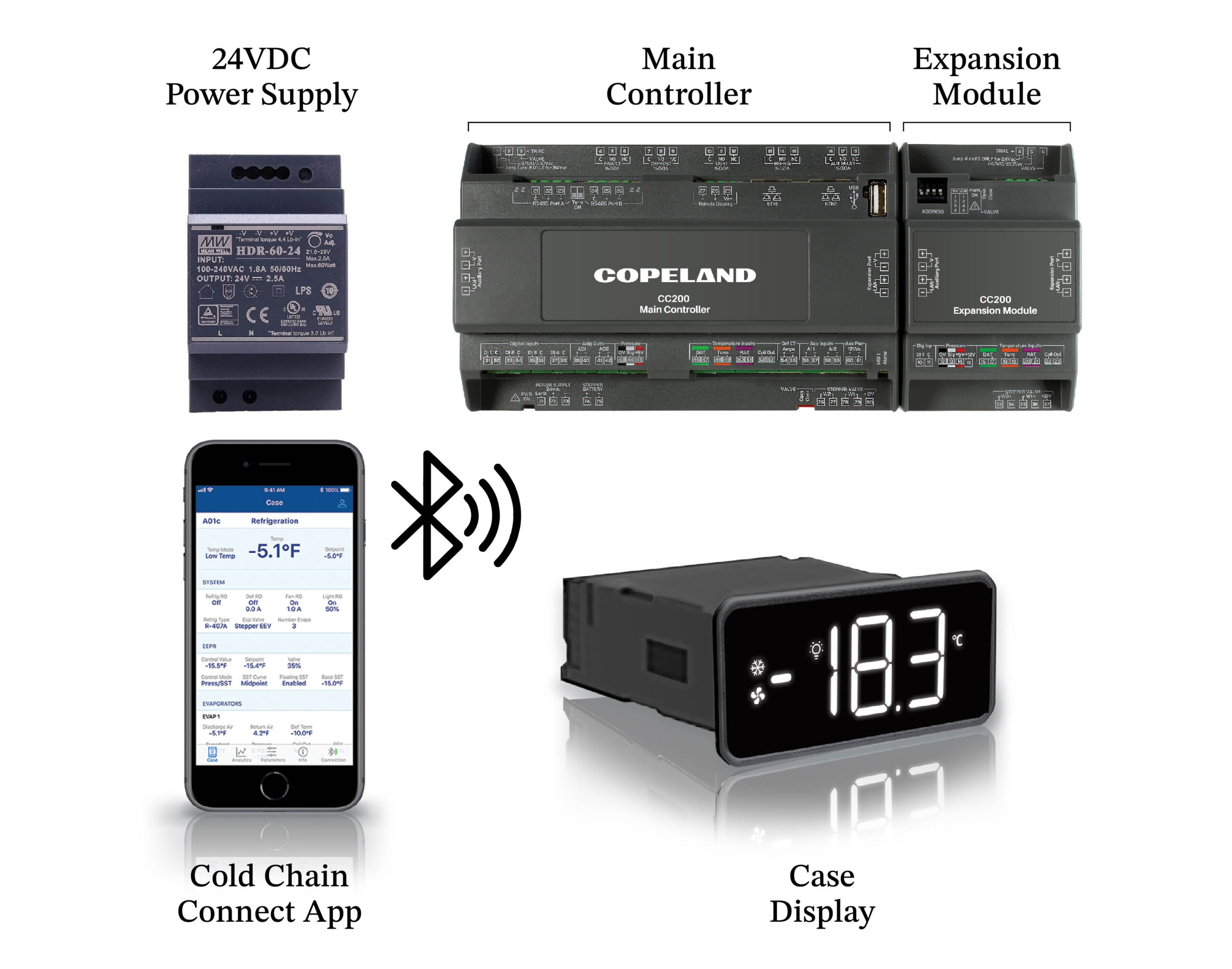
In the first of two recent episodes of the Advanced Refrigeration Podcast, I discussed many of the exciting new advantages the CC200 offers, both for original equipment manufacturers (OEMs) and service technicians.
A smarter approach to case control
The CC200 is an all-new, microprocessor-based case controller with new hardware, software and an up-to-date design approach informed by the needs and capabilities of modern equipment. At the same time, it retains compatibility with existing Copeland controls and sensors (including those produced under the Emerson brand), enables quick and easy upgrades, and allows OEMs to purchase and install fewer components in the control tray than ever before.
The CC200 can control low-, medium- and dual-temperature case designs, case lighting, evaporator fans, defrost heaters, liquid line solenoid valves (LLSVs), stepper valves and pulse-width modulated (PWM) valves — all in one stand-alone case controller. In addition to traditional cases, the solution offers robust support for CO2 (including ultra-low superheat) and will soon be available for A2L systems.
This is Copeland’s first North American case controller with built-in Bluetooth® support. The enhanced connectivity allows technicians to communicate with the system via smartphones and tablets, enabling access to more than 40 system data points and 12 service commands. Technicians can view evaporator superheat, pressure and temperature to evaluate evaporator performance faster and easier than ever before.
Every component is “plug and play”
Another significant change is the ability to power the main CC200 controller, expansion modules and displays with a single power supply through built-in connectors. The case controller can easily accommodate up to three evaporator coils per display case simply by adding plug-in expansion modules.
Expansion modules directly plug into the CC200 side Expansion Port connector, which overcomes the need to run separate wiring for power and communication. This helps clean up the control tray and eliminates the chance of accidentally crossing power and communication wiring.
Every connecter on the controller is also “pluggable”. We all know what it’s like to work in a confined electrical tray; nothing ever seems to be oriented in a friendly direction for a screwdriver, so all the connectors can simply be unplugged if a controller swap or wiring change is needed. In addition, there are
An Onboard 2 port switch allows cases to be connected with a single CAT5 or CAT6 cable, further simplifying communication wiring while increasing speed and reliability compared to RS-485 based protocols. Color-coded analog inputs and intuitively labeled output and valve connectors allow fast and efficient installation and easier troubleshooting. The transducer connector color coding also matches the wire harness for Copeland’s standard pressure transducers.
Hardware innovations give you options (and may help you sleep better)
The podcast hosts were particularly excited about the CC200’s evaporator fan current transducer (CT), which is integrated into the controller’s internal fan relay and requires no external CT to be purchased or wired in. Fan motor current monitoring with this CT allows retailers and technicians to be notified about fan motor failures when they happen instead of days later when the evaporator is already iced up. The CC200 also offers defrost heater monitoring for electric heaters, with an external CT and a dedicated analog input. The combined ability to detect fan motor or defrost heater failures has the potential to prevent iced up evaporators and eliminate a lot of late-night service calls.
Tune in for more details
I highly recommend listening to the first episode in this two-part series to hear a far more in-depth discussion. We’ll review additional insights from the second episode — including the Cold Chain Connect app, integration with E2 and E3 controllers, and other technician-friendly features — in an upcoming blog. You can also visit the CC200 case controller webpage to access a complete overview of the CC200 solution, real-world case study data and other helpful resources.
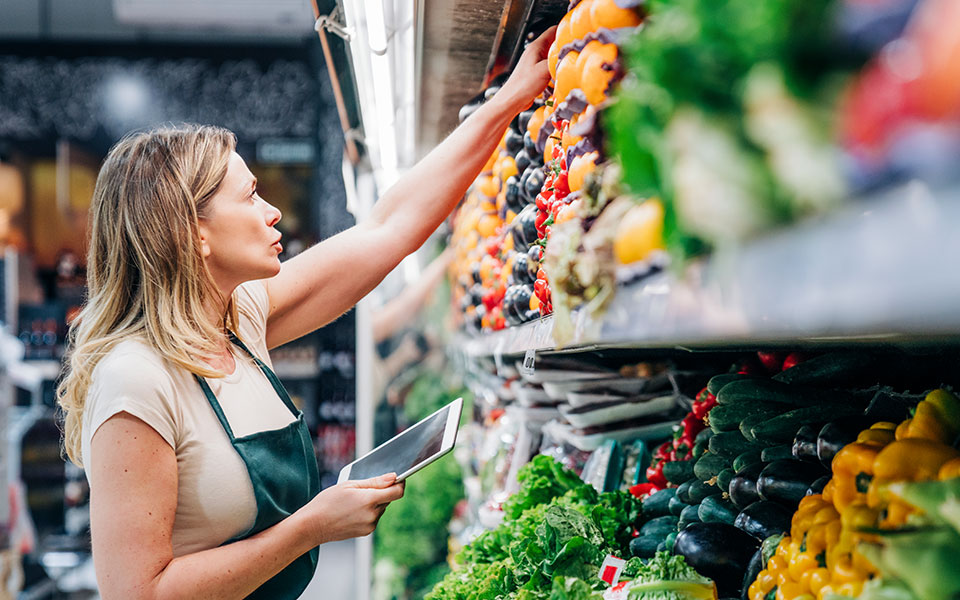
8 proven strategies for rigorous cold chain management
Preparing for the approval and safe use of A2Ls in commercial refrigeration applications...
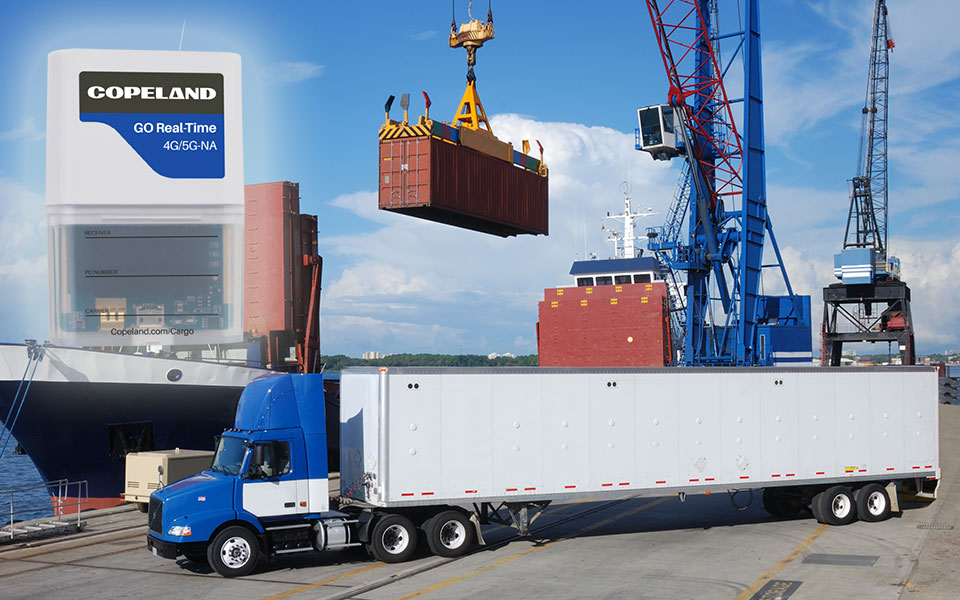
Protection for high-value shipments just got even better
We’re excited to announce the release of Copeland’s newest real-time tracker, the GO Real-Time...
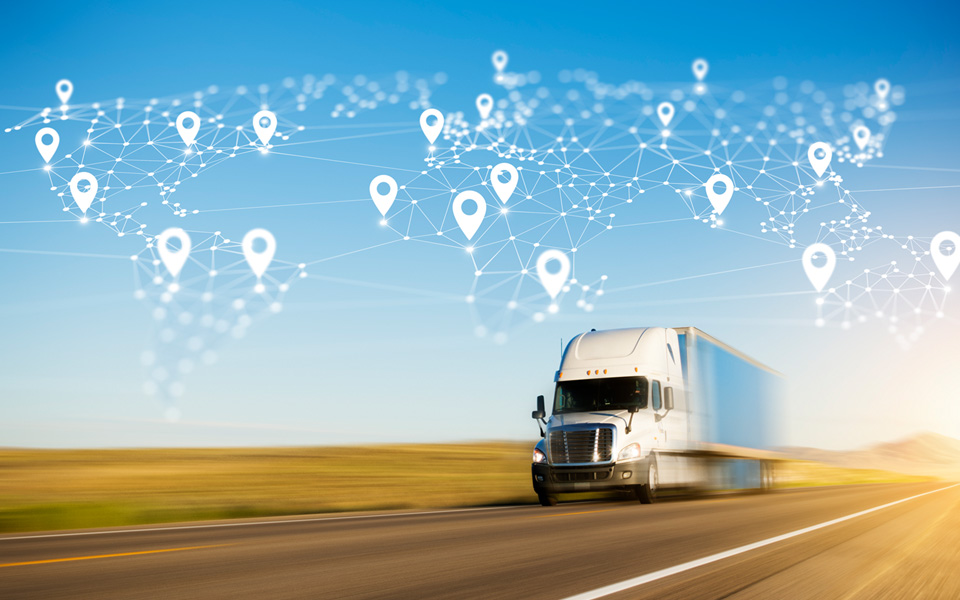
Three proven strategies to prevent cargo theft
The over-the-road (OTR) transport industry is experiencing a surge in cargo thefts. As thieves...