*On June 1, 2023 Emerson’s Climate Technologies business became a new standalone company – Copeland. Though our name has changed, we are building on more than a century of HVACR innovation and industry leadership, and Copeland continues to offer the same products, industry stewardship, and learning opportunities you’ve grown to trust. Information found on this webpage posted before June 1, 2023 may contain our old name or branding, but you can be at ease knowing it was created with the knowledge and expertise of Copeland.
This blog summarizes an article from our E360 program, entitled “Technological Transformation.” Click here to read it in its entirety.

Today’s commercial refrigeration market faces a number of challenges, some of the more prominent being a surplus of regulations, a shortage of qualified technicians, and a consumer base demanding fresh, premium quality foods. Commercial refrigeration manufacturers have maximized their efforts to develop technological solutions that help store operators achieve compliance, sustainability and profitability goals.
This technological transformation starts with the use of electronic controls at the individual component, system and facility/supervisory levels. These controls serve as the brains of new equipment, typically relying on sensors to measure environmental conditions pertaining to mechanical operation. Here’s a closer look at the different levels of electronic controls:
-
- Component controls: integrate with a certain component, like a compressor, to maintain efficiency and identify operational issues
- System controls: operate multiple components within a system, such as a valve, compressor and fan, to control, direct and optimize system-level efficiencies
- Supervisory controls: coordinate the operation of multiple systems, like refrigeration, HVAC and lighting, allowing for component and system controls to communicate their conditions for store operators or technicians to assess and interpret
The second important technological development is the emergence of new electro-mechanical components that perform specific functions within the refrigeration cycle, including compressors, valves and fans. These can either be self-contained or in two separate components that are installed together.
An exception is scroll compression technology, which doesn’t necessarily need electronic controls to address many operator challenges. The inherent benefits combine multi-refrigerant capabilities with reliable operation and energy efficiency.
However, the addition of controls elevates scroll compressor benefits. One of these is the ability to modulate capacity, enabling precise temperature control and improved energy efficiencies. In fact, capacity modulation is so effective in reducing energy consumption that some utilities offer incentives for operators to make the transition. New electronic expansion valves also improve system efficiencies, providing precise control of refrigerant flow and system superheat using today’s new class of lower-GWP, HFC refrigerant alternatives.
The advanced diagnostic capabilities help operators prevent system failures, limit reliance on technicians, and take maintenance operations into their own hands. Even when maintenance is required, these diagnostics greatly improve the servicing process. Remote access allows technicians to quickly diagnose and fix refrigeration system errors, improving a technician’s effective service capabilities and reducing maintenance costs.
The adoption of these technologies allows operators to address compliance and operational challenges, all while protecting profitability. As the commercial refrigeration industry begins to see new challenges and regulations arise, the expanding capabilities of refrigeration technology and controls will ease the worries of operators and make problem-solving easier.
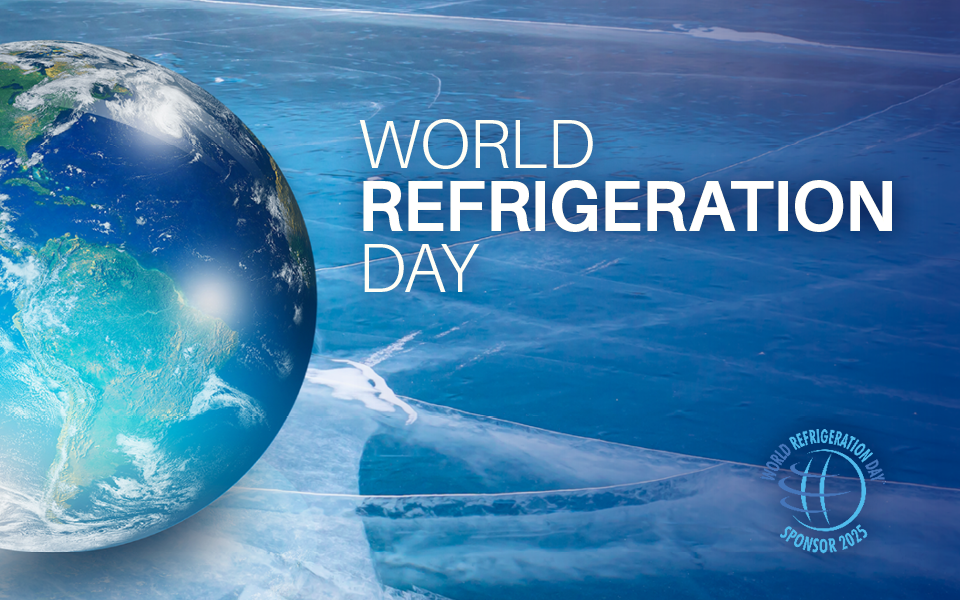
Celebrating World Refrigeration Day 2025
Electrical component considerations for A2L system safety Heating, ventilation, air conditioning...
A2L Refrigeration Overview — Systems, Safety and Servicing Considerations
*On June 1, 2023 Emerson’s Climate Technologies business became a new standalone company –...
Servicing the Next Generation of Lower-GWP Refrigerants
*On June 1, 2023 Emerson’s Climate Technologies business became a new standalone company –...