Electrical component considerations for A2L system safety
As a new refrigerant category in the commercial refrigeration sector, the A2L “lower flammability” classification comes with unique considerations. Specifying engineers and contractors need to know the new requirements and risk mitigation measures that apply to A2Ls, both to ensure safety and alleviate retailers’ concerns.
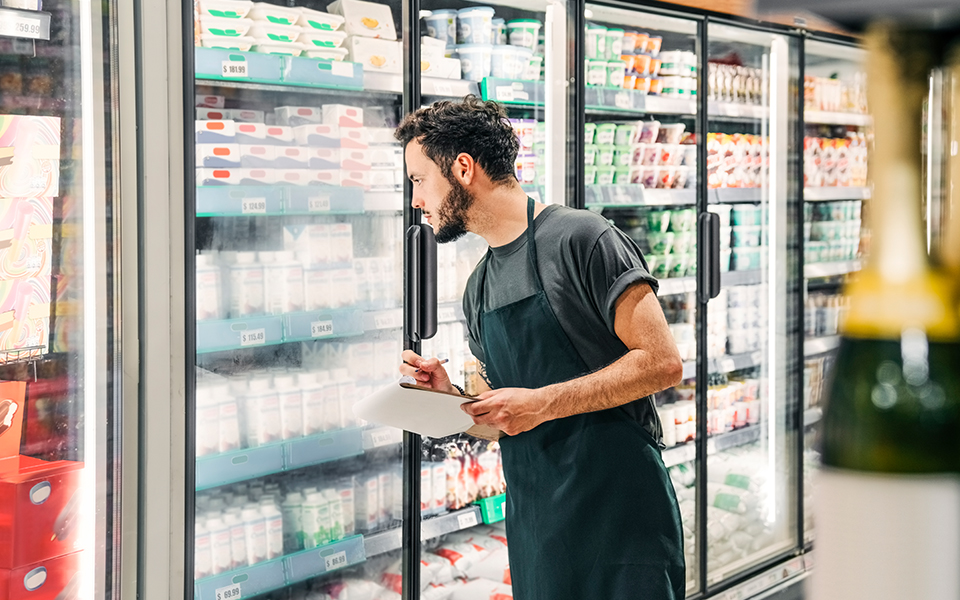
As I noted in a recent article for ACHR News, ensuring electrical system safety compliance is a chief design consideration with A2L-optimized equipment because electrical sparks or charges could be potential sources of ignition. The Underwriters Laboratories (UL) 60335-2-89, 2nd edition safety standard establishes design strategies based on the lower flammability limit (LFL) of an A2L, which includes charge limit allowances, leak rates and detection requirements. LFL is based on the worst-case formulation (WCF) — or maximum refrigerant burning velocity — of all A2L refrigerants being considered for approval.
Because electrical sparks or charges could be potential sources of ignition, specifying engineers and contractors must be sure that compressors and condensing units use only certified electrical componentry, including:
- Relays/contactors and/or devices used for switching electrical currents on/off
- Controllers
- Variable-frequency drives (VFDs)
- Electrical enclosures (boxes) capable of containing full systems
Design strategies
It’s important to understand the difference between protected and unprotected systems, as well as the requirements for achieving A2L system certification in each:
- Protected systems are those in which no part of the cooling system is inside the food storage compartment. They must be designed to ensure refrigerant leaks will not pose a fire or explosion hazard. This is typically achieved by containing the refrigerant system in an enclosure so that leaked gas can’t reach the food storage area.
- Unprotected systems are appliances in which at least one part of the cooling system is placed inside a food storage compartment. These systems must be designed with additional safety measures because a refrigerant leak could create conditions for an explosion near electrical components.
For unprotected systems, A2L safety compliance and/or certification may be achieved either through individual component-level certification or at a higher level that encompasses the entire system in an electrical enclosure. Only one certification approach is necessary to achieve compliance.
Component-level considerations
For component-level certification, electrical components, relays or devices must adhere to tight enclosure tolerances. Essentially, the maximum size of openings (i.e., holes) must be small enough that sparks or flames can’t escape.
There are certification exceptions for certain relays and switching devices that are not considered ignition sources. These are deemed inherently compliant with the UL standard and don’t require testing. (See the E360 Outlook report linked below for full details of the criteria.)
Considerations for enclosures and systems
For electrical enclosures and/or system-level certification, the UL standard provides a comprehensive range of testing requirements to certify compliance with its flame-arrest enclosure verification standard. A flame-arrest enclosure is defined as a “device or assembly enclosing components with electrical contacts that are made and broken, or similar devices which can become a source of ignition.”
A qualifying enclosure must be able to withstand the internal ignition of leaked A2L refrigerant vapor without suffering damage and transmitting flame to an external concentration of the same refrigerant. Note: qualified individual electrical components contained within a flame-arrest enclosure are not considered sources of ignition.
If all openings in the flame-arrest enclosure comply with the Annex 101.DVM standard, the enclosure is considered compliant.
Surface temperature limits
Regardless of all other testing and certification measures, the surface temperature limits of affected electrical devices must also be factored into the A2L safety equation. (See Table 1.)
Refrigerant | Safety Group | Lower Flammability Limit (LFL) | Auto-Ignition Temperature (AIT) | Maximum Surface Temperature (AIT – 100 °K) |
R-454C | A2L | 0.291 kg/m³ | 413 °C | 313 °C |
R-454A | A2L | 0.281 kg/m³ | 426 °C | 326 °C |
R-455A | A2L | 0.432 kg/m³ | 497 °C |
397 °C
|
Table 1: A2L flammability characteristics and maximum surface temperatures
Refrigeration potential
A2L refrigerants have vast potential in the commercial refrigeration sector, delivering a unique combination of lower global warming performance (GWP), high performance and energy efficiency. By using equipment and components optimized and certified for A2L refrigerants, specifying engineers and contractors can help their retail customers safely transition to these emerging refrigerants.
Copeland is committed to developing safe, A2L-optimized compression, controls and electrical componentry to give specifying engineers and contractors a range of system options from which to support their customers’ next-gen equipment strategies. We have the application and engineering expertise — and flammable refrigerant testing facilities — to help maximize equipment safety using the next generation of low-GWP refrigerants.
To learn more about A2L safety compliance criteria, including certification exceptions and safety standards for VFDs, download our full E360 Outlook report: Electrical component considerations for A2L system safety.
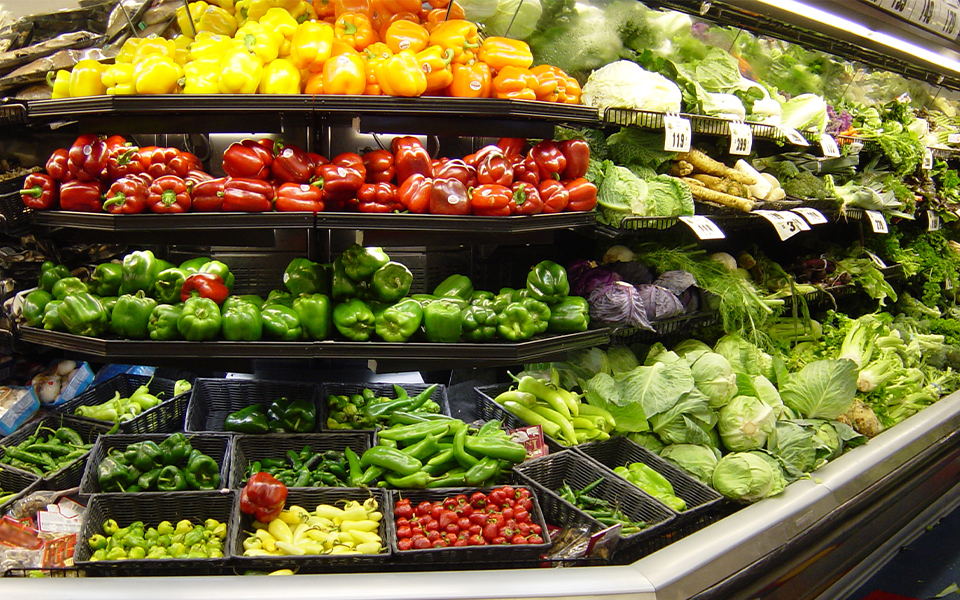
Facility Health Score Insights Program Transforms Enterprise Maintenance
Leveraging refrigeration performance data drives food retail cost reductions. Maintaining proper...
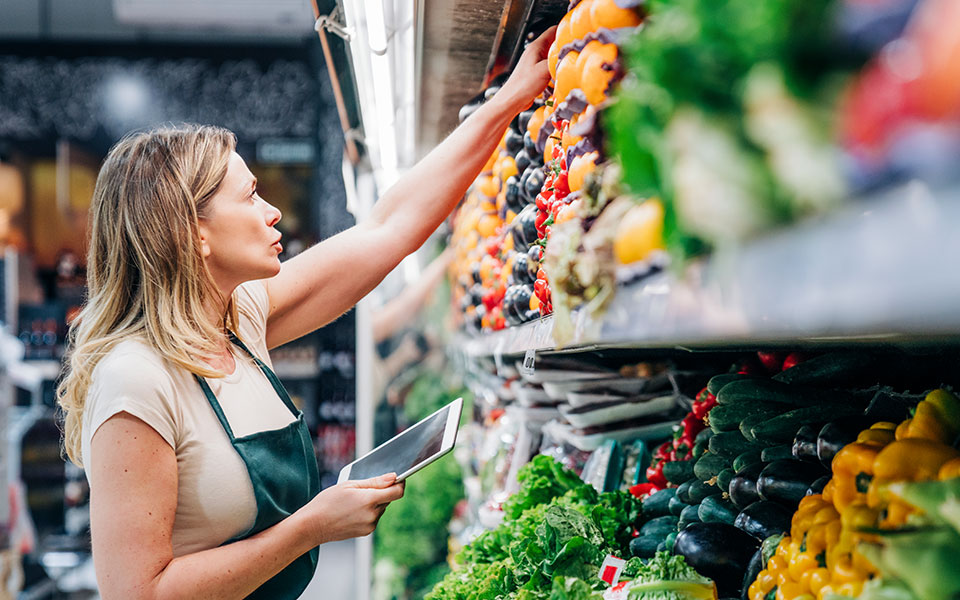
8 proven strategies for rigorous cold chain management
Preparing for the approval and safe use of A2Ls in commercial refrigeration applications...
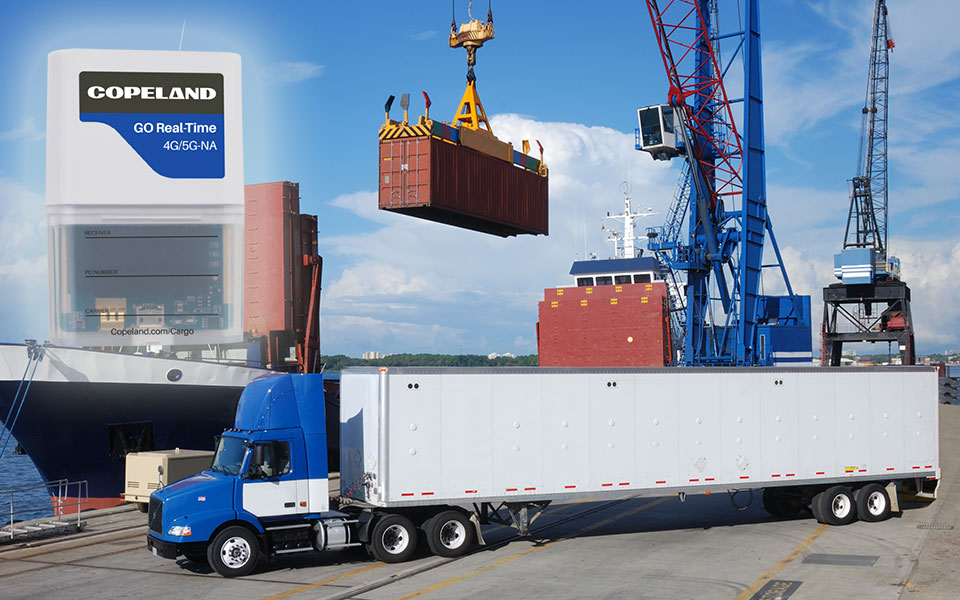
Protection for high-value shipments just got even better
We’re excited to announce the release of Copeland’s newest real-time tracker, the GO Real-Time...