*On June 1, 2023 Emerson’s Climate Technologies business became a new standalone company – Copeland. Though our name has changed, we are building on more than a century of HVACR innovation and industry leadership, and Copeland continues to offer the same products, industry stewardship, and learning opportunities you’ve grown to trust. Information found on this webpage posted before June 1, 2023 may contain our old name or branding, but you can be at ease knowing it was created with the knowledge and expertise of Copeland.
Proactive refrigerant management isn’t just good for the environment. It is also sound business practice. I was recently interviewed by ACHR’s The News magazine on the Environmental Protection Agency’s (EPA) partial rollback of Section 608 provisions for appliance leak repair and maintenance. You can read the full article here and more on our perspective below.

In February, the EPA eliminated leak repair and maintenance requirements on appliances containing 50 or more pounds of substitute refrigerants, such as hydrofluorocarbons (HFCs). As a result, equipment owners are no longer required to:
-
- Repair appliances that leak above a certain level
- Conduct verification tests on repairs
- Periodically inspect for leaks
- Report chronically leaking appliances to the EPA
- Retrofit or retire appliances that are not repaired
- Maintain related records
But just because these leak repair provisions are no longer required doesn’t mean food retailers should ignore these best practices. There is a price to pay for refrigerant leakage that extends far beyond environmental damage. Detecting, repairing and even proactively reducing refrigerant leaks will help operators avoid a variety of associated costs.
The high cost of refrigerant leaks
The rollback of legal penalties for refrigerant leaks does not change the math on the operational costs. An average food retail store leaks an estimated 25 percent of its refrigerant supply each year, which can quickly add up to thousands of dollars in lost refrigerant. In addition, retailers must consider the maintenance and equipment costs. Persistently low levels of refrigerant can cause:
-
- Excess compressor wear and tear
- Reduced compressor and system capacities
- Premature system failures
- Double-digit efficiency losses
Left unchecked, even minor leaks can eventually lead to equipment failure. When this occurs, emergency repair costs are often only the tip of the iceberg. Operators may also be looking at revenue loss from food waste, business disruptions and reputational damage.
Proactive refrigeration management
So what can operators do to prevent leaks, even in the absence of federal requirements?
In the near term, they can — and should — implement rigorous leak detection and repair programs. Refrigerant leaks can occur anywhere in a system. Thus, an effective refrigerant leak detection program will combine monitoring, detection and notification.
Multiple technologies are available to support these efforts, including active and passive devices for monitoring and detection. Internet of things (IoT) capabilities allow for remote monitoring, enabling operators to focus on more pressing tasks. And with the integration of data analytics platforms, operators can uncover trends, identify persistent problem areas, and make informed choices about equipment upgrades and replacement options.
Over the longer term, operators can adopt refrigeration architectures that reduce the potential for refrigerant leakage in the first place. Legacy, centralized direct-expansion rack systems are high leak-rate offenders. That shouldn’t be a surprise; with thousands of feet of pipe, hundreds of joints and large refrigerant charges, there are many opportunities for leaks to occur.
In contrast, distributed micro-booster, indoor distributed and outdoor condensing unit (OCU) architectures experience lower leak rates by design. As an added benefit, they offer more options for lower-GWP alternative refrigerant use. This is a crucial advantage for operators who want to position their business for future regulations.
Sustainable best practices
The EPA’s Section 608 leak repair provisions were good for the environment. They are also part of a larger body of best practices for optimizing HVACR equipment. As states take the lead in adopting standards for leak detection and control, operators may find the rollback of these regulations to be short-lived.
Emerson is proud to take a lead in developing sustainable and cost-effective refrigeration systems and supporting technologies. Operators and original equipment manufacturers count on us to deliver strategies and solutions that anticipate emerging trends and regulations. From pioneering refrigeration architectures to refrigerant leak detection tools, we are committed to providing operators with the capabilities to meet their sustainability and operational goals today and into the future.
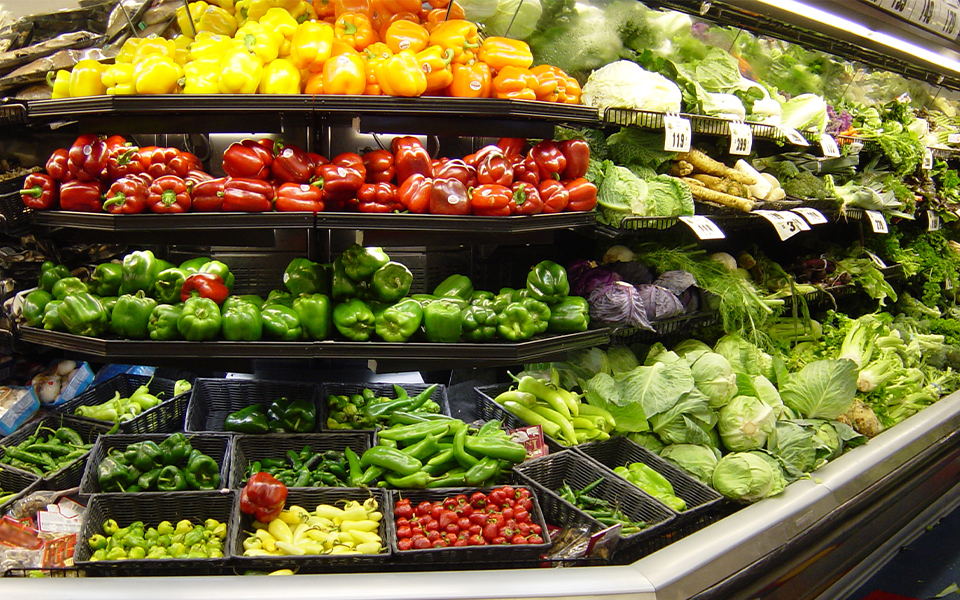
Facility Health Score Insights Program Transforms Enterprise Maintenance
Leveraging refrigeration performance data drives food retail cost reductions. Maintaining proper...
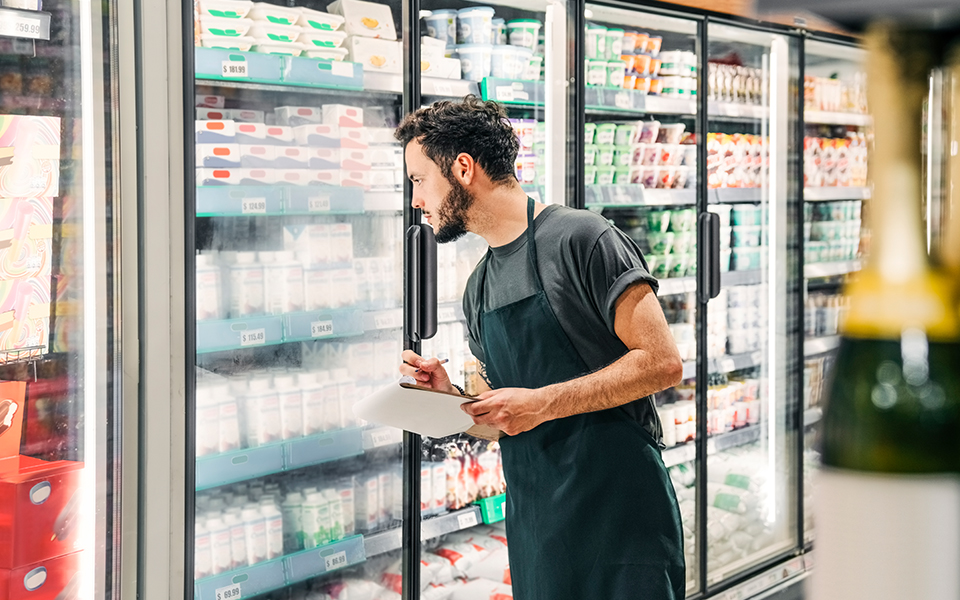
Electrical component considerations for A2L system safety
Electrical component considerations for A2L system safety As a new refrigerant category in the...
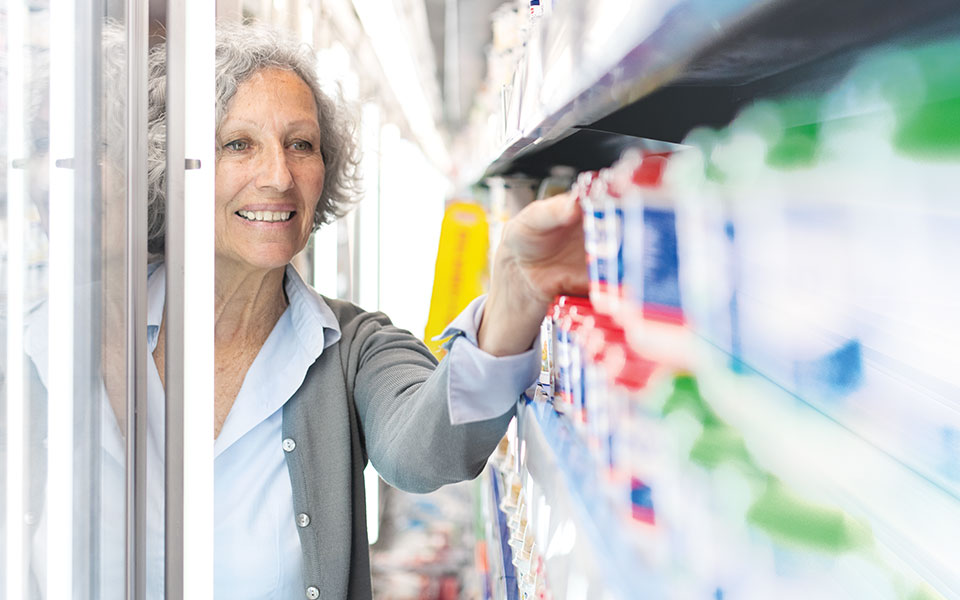
A2L refrigerant regulation updates: what you need to know today
Preparing for the approval and safe use of A2Ls in commercial refrigeration applications The move...