*On June 1, 2023 Emerson’s Climate Technologies business became a new standalone company – Copeland. Though our name has changed, we are building on more than a century of HVACR innovation and industry leadership, and Copeland continues to offer the same products, industry stewardship, and learning opportunities you’ve grown to trust. Information found on this webpage posted before June 1, 2023 may contain our old name or branding, but you can be at ease knowing it was created with the knowledge and expertise of Copeland.
CO2 is an emerging natural refrigerant alternative, but it poses a sharp learning curve for technicians in the U.S. I recently authored an article in RSES Journal that explains why contractors will need to start enhancing their knowledge and adapting their skillsets now to prepare for future servicing needs. You can read the full article, “Fundamentals of CO2 Refrigeration,” here.

Why Contractors Need to Prepare Now for the Coming CO2 Refrigerant Revolution
As the drive to replace hydrofluorocarbon (HFC) refrigerants with lower-GWP (global warming potential) alternatives heats up, CO2 (or refrigerant R-744) is a proven natural option that is experiencing wider adoption in the U.S. — particularly in large centralized systems.
Natural refrigerants — so named because they occur naturally in the environment — also include both propane and ammonia. But for larger-format supermarket operators seeking an all-natural, environmentally friendly option, CO2 checks all the boxes. It’s nonflammable and nontoxic. It presents no threat to the ozone layer. And it meets every current and known future regulatory requirement. In addition, whereas R-404A has a GWP of 3,922, CO2 has a GWP of 1.
While CO2 refrigeration architectures have been successfully deployed in European commercial and industrial settings for nearly two decades, they are a relative newcomer to the U.S. That’s set to change as more operators face regulatory mandates or have stated sustainability objectives.
This will pose a sharp learning curve for many refrigeration contractors and service technicians, especially those who aren’t familiar with the peculiarities of CO2, or the transcritical CO2 booster architecture they’re most likely to encounter soon.
Understanding CO2’s unique properties
When servicing transcritical CO2 booster systems, technicians will need to account for factors that they have never needed to consider with HFC systems. CO2 has a much lower temperature at atmospheric pressure than HFCs. It also has a higher saturation point, as well as higher operating and standstill pressures. Understanding how these characteristics impact system operation servicing requirements and system performance is essential:
- Low critical point.CO2’s very low critical point (at 1,056 psig or 87.8 °F) determines its modes of operation; the system will operate in subcritical mode at low ambient temperatures and transcritical mode at higher ambient temperatures.
- High triple point.At 61 psig, CO2’s triple point — where the refrigerant’s solid, liquid and vapor phases coexist — is very high. If system pressures reach the triple point, the refrigerant will turn to dry ice, which affects system performance and presents a potential safety hazard.
- Rapid pressure rise.During power outages, CO2 pressures can rise quickly. Pressure-relief valves will release the refrigerant charge when it exceeds acceptable pressures, but this can increase the risk of product loss. To prevent system evacuation, CO2 systems often are designed with an auxiliary cooling system.
- Vapor to liquid charging.CO2 systems typically use both liquid and vapor to charge, requiring careful coordination to prevent the formation of dry ice.
Transcritical CO2 systems are specifically designed to manage its high pressures and maximize its full potential. Because this system design represents a completely different approach than typical HFC systems, specialized training is required to service these systems and understand their supporting technologies, which typically include high-pressure controllers, electronic expansion valves, pressure transducers and temperature sensors.
Finding the right educational resources
Contractors and technicians who want to add CO2 servicing to their qualifications would do well to start educating themselves now. All signs indicate that its adoption in the U.S. will accelerate in the near future. Given CO2’s peculiarities and unique system design strategies, it is imperative that technicians familiarize themselves with the refrigerant and the operation of a CO2 system.
At Emerson, we are leading the industry in CO2 refrigeration system innovation. But we don’t just offer a full suite of CO2 refrigeration system components. We also are dedicated to helping contracting businesses ensure their service technicians understand how to safely install, commission and service these systems. Our Educational Services team offers a comprehensive CO2 training curriculum for contractors seeking to learn more about working with this emerging refrigerant alternative.
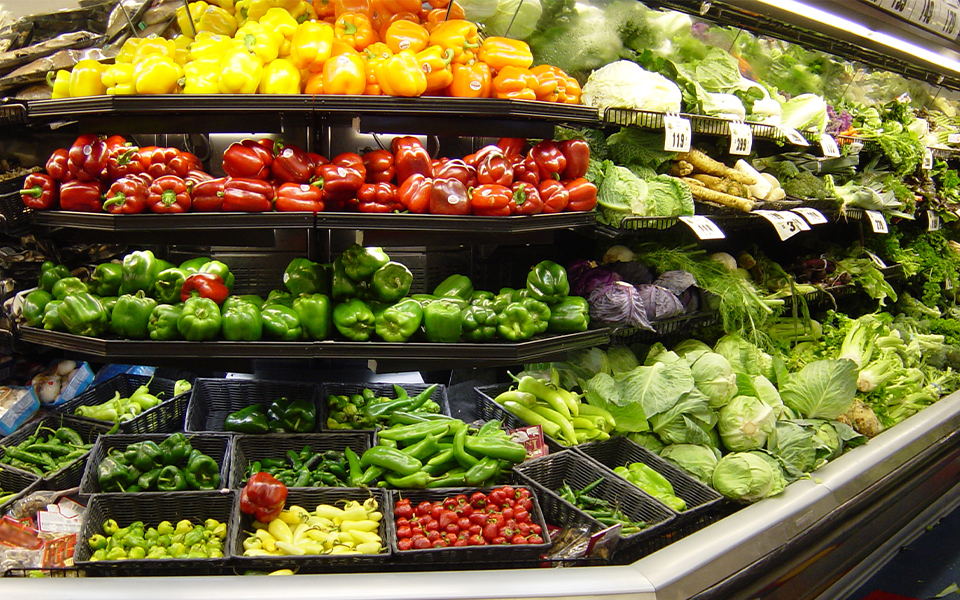
Facility Health Score Insights Program Transforms Enterprise Maintenance
Leveraging refrigeration performance data drives food retail cost reductions. Maintaining proper...
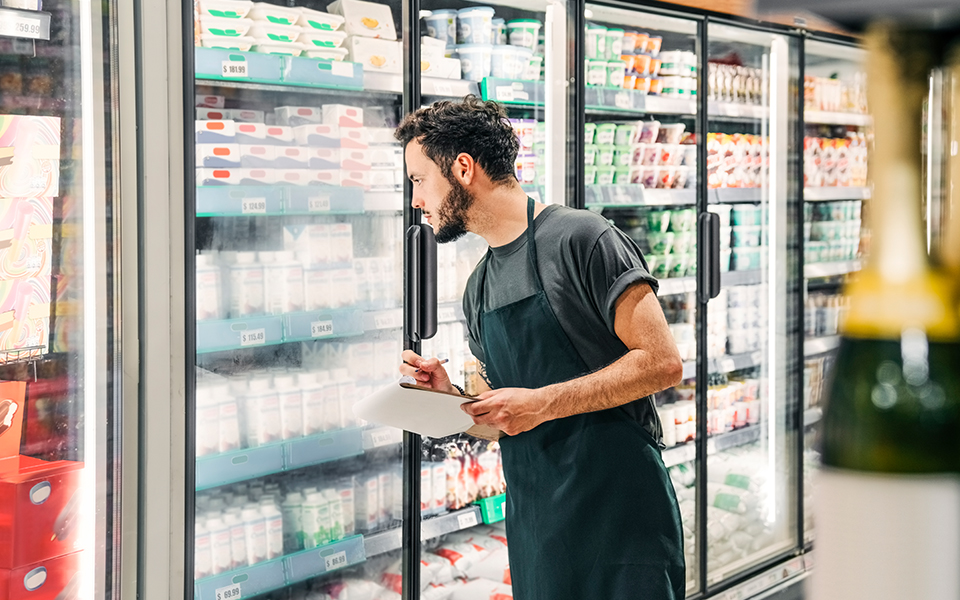
Electrical component considerations for A2L system safety
Electrical component considerations for A2L system safety As a new refrigerant category in the...
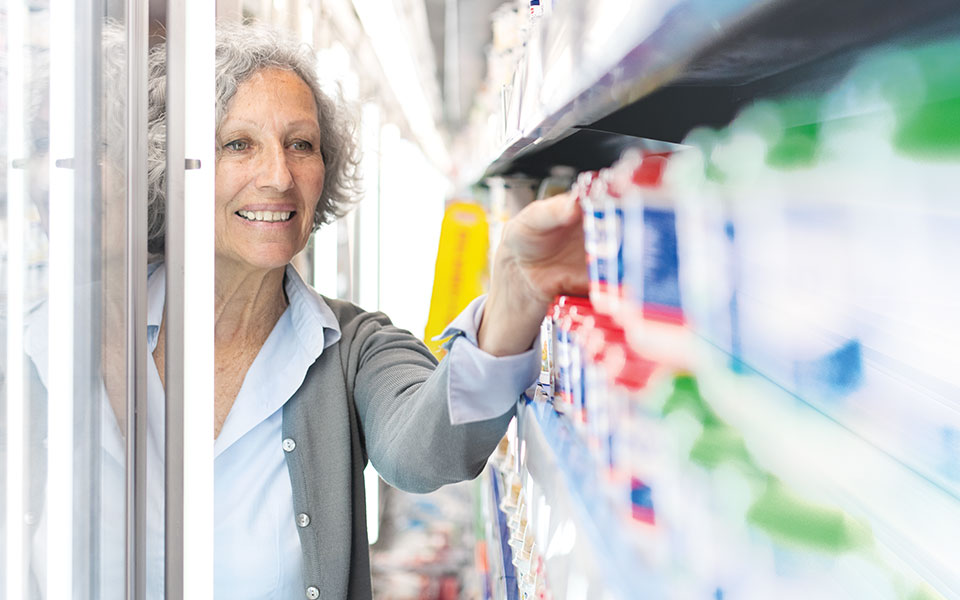
A2L refrigerant regulation updates: what you need to know today
Preparing for the approval and safe use of A2Ls in commercial refrigeration applications The move...