*On June 1, 2023 Emerson’s Climate Technologies business became a new standalone company – Copeland. Though our name has changed, we are building on more than a century of HVACR innovation and industry leadership, and Copeland continues to offer the same products, industry stewardship, and learning opportunities you’ve grown to trust. Information found on this webpage posted before June 1, 2023 may contain our old name or branding, but you can be at ease knowing it was created with the knowledge and expertise of Copeland.
Refrigerant leaks are a universal challenge for U.S. supermarket operators. These leaks are not only costly from an operational perspective, but emissions of hydrofluorocarbon (HFC) refrigerants also contribute to global warming. Today, commercial refrigeration contractors play a significant role in helping operators to implement best practices to reduce and even prevent refrigerant leaks. I recently contributed to an ACHR The NEWS article where I discussed strategies for leak detection and mitigation best practices for supermarket refrigeration systems.
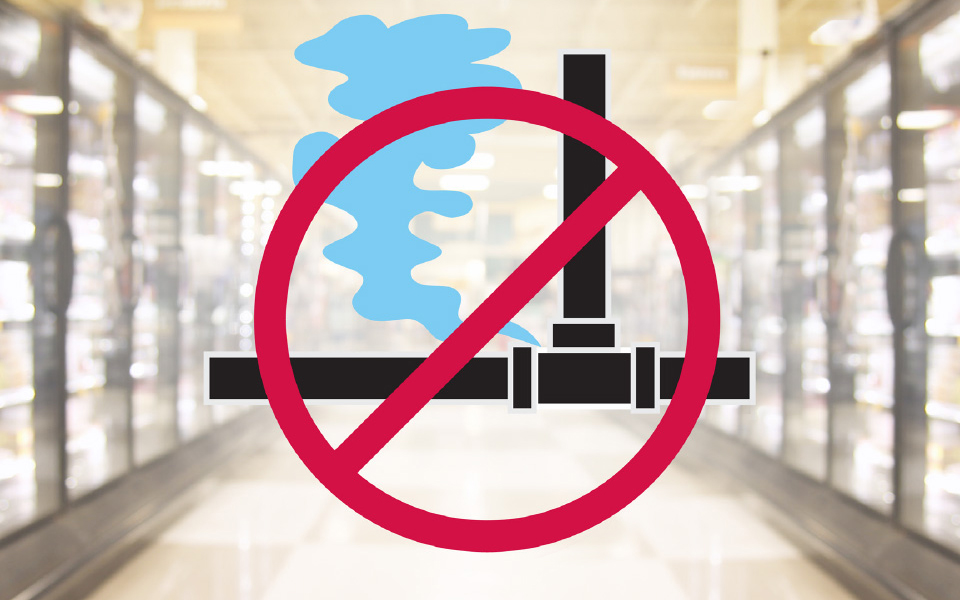
Understand root causes
Although refrigerant leaks are much more common in large, centralized systems, it’s not as if contractors or operators simply accept leaks as a design limitation. On the contrary, when a refrigeration system is first installed and commissioned, it operates at peak performance. But over time, systems inevitably drift from their commissioned performance baseline, contractors perform repairs to keep systems running, and the potential for leaks can start to rise if a system is not properly maintained and managed.
For a contractor’s perspective on refrigerant leaks, the NEWS also interviewed Todd Ernest, CEO and founder of Climate Pros, a comprehensive commercial refrigeration and HVAC firm with offices in more than 40 states. Ernest agreed that while leaks are a common problem, nearly half of the stores serviced by Climate Pros do not have refrigerant leaks. One common problem that they discovered is that many stores still use the same copper lines and systems that were installed decades ago. Though durable, copper isn’t intended to last forever — and original insulation and mounting hardware will often eventually wear down.
Similarly, mechanical room cleanliness is also essential for helping contractors to identify leaks. Compressor racks, air-cooled condensers, remote headers, walk-in evaporator coils and other components should be kept free of oil and dirt. Corroded steel components should be removed and/or painted with a rust-inhibiting paint to help prevent future corrosion.
Check for leaks
As I explained in the article, service technicians should conduct refrigerant leak checks at regular intervals, depending on the system size or type. For large, centralized systems, this should usually be approximately every 30–60 days. An effective leak detection program should include three key elements:
- Accurate detection methods
- Reliable notifications
- Continuous monitoring for system leaks
Contractors should recommend the installation of a refrigerant leak monitoring, notification and alarm system to ensure the detection of any leaks between regular leak inspections. Detection devices should also be installed in leak-prone locations, such as refrigeration racks and display cases, to monitor the concentration of refrigerants in the air.
By integrating these devices into Emerson’s Lumity™ supervisory control platform, designated store staff and/or service technicians can be alerted when a leak occurs. This powerful facility management system enables continuous monitoring of refrigeration data to help retailers correlate the leaks with respect to different sections of the system or specific maintenance events.
Ernest added that it’s standard protocol for his technicians to perform a leak check every time they go into a store — regardless of the purpose of the actual service call.
Promptly repair leaks
Today’s leak detection devices make it easier to pinpoint leak sources, but it’s important to remember that in many cases, the first refrigerant leak found in a system may not be the only one — or even the largest.
A quick response is most important after detecting a leak to mitigate its impact upon system performance and minimize the associated economic costs. Supermarkets should establish proper leak detection response protocols and institute proactive measures.
If persistent leaks continue, even at lower leak rates of 20%, supermarkets could lose approximately 700 pounds of R-404A annually. At $7 per pound, that equates to a yearly expense of nearly $5,000 — in addition to any potential costs associated with compliance, environmental consequences and overall deterioration of system performance.
A methodical approach can help to achieve all-important early detection and an overall reduction in refrigerant leaks. The NEWS article concluded with these 10 tips:
- Perform a leak check on every service call. Conduct refrigerant leak checks at regular intervals, ideally every 30–60 days for large centralized systems.
- Periodically replace copper lines as well as insulation and mounting hardware.
- Keep refrigeration racks and mechanical rooms as clean as possible in order to spot leaks more easily.
- If one leak is found, it may not be the only one, so check the entire system thoroughly.
- Once all leaks have been repaired, confirm that refrigerant levels have stabilized, indicating there are no additional leaks elsewhere in the system.
- Install a refrigerant leak monitoring, notification and alarm system to detect leaks between regular leak inspections.
- During refrigeration system installation, use proper securing mechanisms for piping and the correct piping techniques.
- Perform a nitrogen purge and pressure test with every new installation to ensure no leaks are present.
- Establish leak detection response protocols and proactive measures to minimize or eliminate leaks altogether.
- Implement a refrigerant tracking system to identify significant leaks.
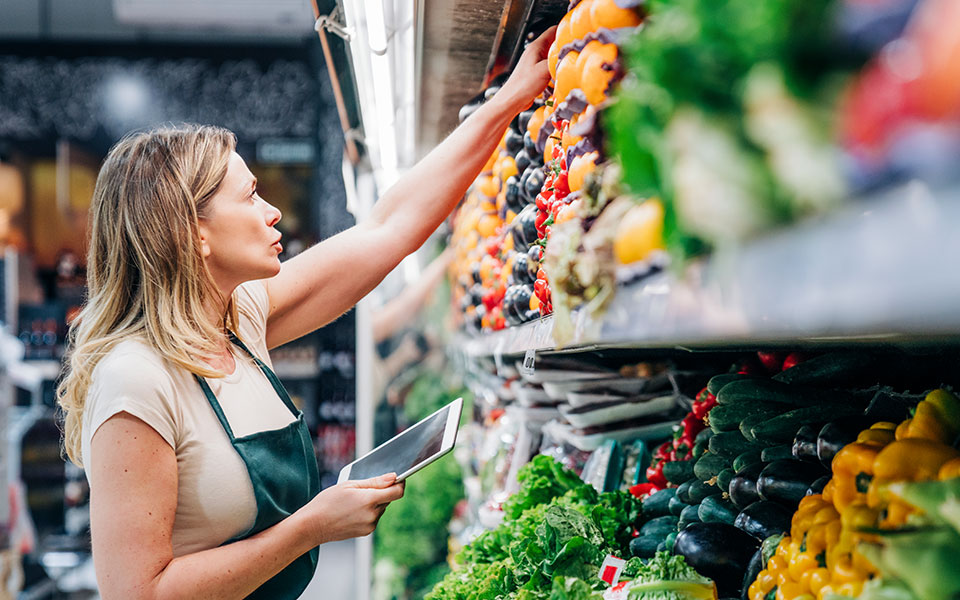
8 proven strategies for rigorous cold chain management
Preparing for the approval and safe use of A2Ls in commercial refrigeration applications...
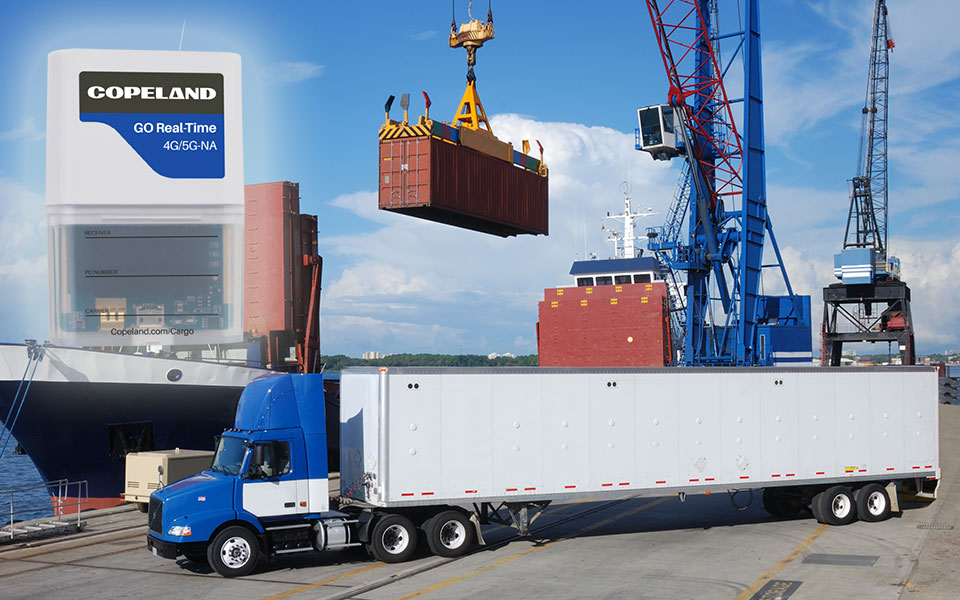
Protection for high-value shipments just got even better
We’re excited to announce the release of Copeland’s newest real-time tracker, the GO Real-Time...
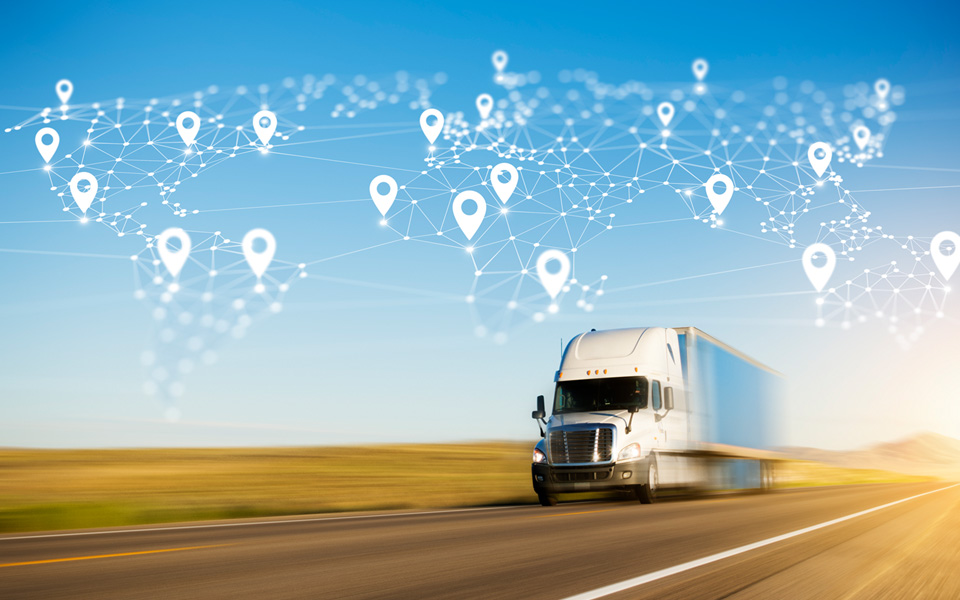
Three proven strategies to prevent cargo theft
The over-the-road (OTR) transport industry is experiencing a surge in cargo thefts. As thieves...