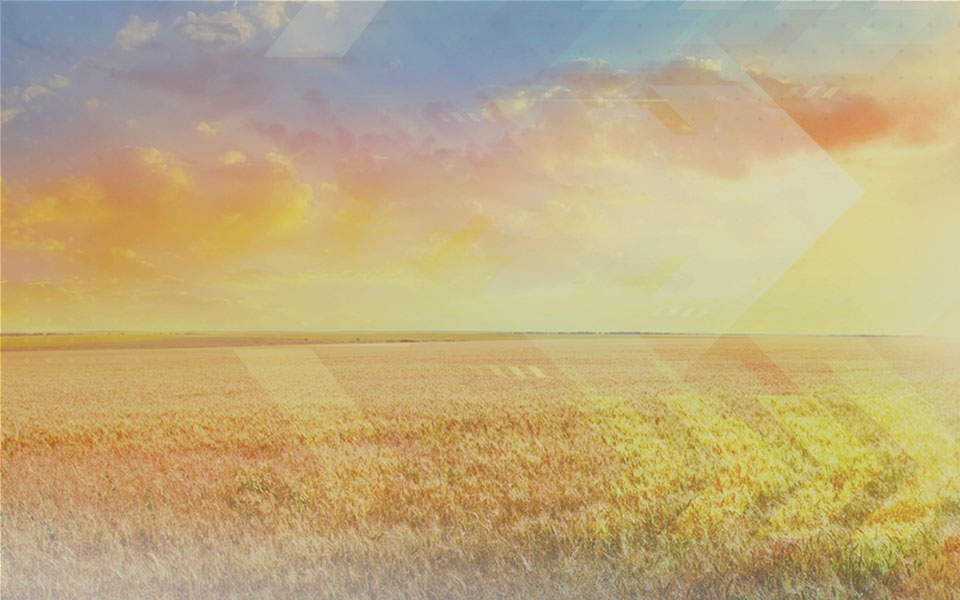
Strong Sustainability Tailwinds Drive CO2 Growth in the Industrial Sector
Natural refrigerants have a long history in the industrial refrigeration sector. Chosen for its excellent performance characteristics and operational reliability, ammonia (R-717) has been an industrial refrigerant workhorse for many decades. Renewed concerns about its toxicity have prompted new legislation to ensure safety, potentially adding to installation complexities. But ammonia’s not the only natural refrigerant option in the industrial sector; CO2 (R-744) is rapidly emerging as a viable, lower-risk alternative.
Corporate sustainability goals and global refrigerant regulations have pushed CO2 into the industrial spotlight in recent years. As it becomes more certain that hydrofluorocarbon (HFC) refrigerants will be phased down, the days of using legacy refrigerants (such as R-404A, HFC-134a, R-448A/449A and R-22) are seemingly numbered.
Natural refrigerants ammonia and CO2 are among the most likely “future-proof” options to take their place in the industrial market. With its small charge limitations, the other leading natural refrigerant R-290 (i.e., propane) is better suited for self-contained commercial refrigeration applications. Regardless, CO2 eliminates the toxicity concerns and application complexities of ammonia and the potential flammability of R-290.
CO2 compression and system technologies are evolving to meet the modern demands of industrial refrigeration. As industrial operators phase in their next-gen equipment strategies, CO2 is poised for significant growth.
Market trends favor the emergence of CO2
The industrial refrigeration landscape is being shaped by a multitude of dynamic market and regulatory forces. If we step back and review recent developments, we can see how the industry is evolving toward CO2.
The HFC phasedown is well underway.
After the banned production of the commonly used hydrochlorofluorocarbon (HCFC) R-22 and other HCFCs under the Montreal Protocol. Following the guidance of the Kigali Amendment to the Montreal Protocol, and a similar F-gas regulation in the E.U. 5 years earlier, The American Innovation and Manufacturing (AIM) Act of 2020 provided the Environmental Protection Agency (EPA) authority to address hydrofluorocarbons (HFCs).
Although the EPA’s Technology Transitions rule (2023) may have given the industrial sector more time than expected to transition to lower-GWP refrigerants in new equipment, the HFC phasedown is moving forward as planned. By the end of the decade, a 150 GWP limit will apply nationally, while some states such as New York and California are targeting much lower GWP limits. These measures will essentially take higher-GWP refrigerant options off the table for any long-term industrial plans.
Ammonia safety standards are tightening.
The EPA recently finalized its risk management program (RMP) for industrial refrigeration applications, which includes safety provisions for ammonia. Enforcement is expected take effect on May 11, with the stated goals of:
- Improving process safety
- Assisting in planning, preparedness and response to RMP-reportable accidents (will require the implementation of third-party audits)
- Increasing public awareness of chemical hazards at regulated sources
Occupational Safety and Health Administration (OSHA) regulations have strict documentation requirements, and new provisions will soon be introduced to ensure application safety via its process safety management (PSM) initiatives. Of note, operations using significant charges of ammonia will have additional refrigerant management requirements, which will likely increase the costs of these programs.
Similar requirements are already in place in certain states, cities and authorities having jurisdiction (AHJ) — where ammonia application approval is becoming even more difficult due to safety concerns in densely populated areas. Adhering to these requirements may be cumbersome to operators seeking to transition to ammonia or expand their existing ammonia operations.
Commercial adoption drives CO2 growth in the industrial sector.
In the commercial refrigeration sector, CO2 is expected to grow exponentially over the next five years. Its popularity has helped to create a pull-through effect into the industrial sector. As an already approved and field-tested refrigerant, CO2 offers a proven, sustainable alternative that can eliminate regulatory uncertainties and ammonia safety concerns.
R-744’s high pressures and unique characteristics introduce new operational and technological strategies, including subcritical and transcritical (or supercritical) modes of operation. As has been demonstrated in commercial systems, these caveats can be easily managed with robust design technologies and system controls.
Some heavier commercial-grade CO2 compressors have entered the light industrial market over the past five years in large-scale CO2 booster systems. Though effective, their 500-ton feasibility range revealed a critical need for industrial-grade CO2 compression solutions.
Purpose-built compression for industrial CO2 applications
With decades of innovations in the industrial sector — including in ammonia applications — Vilter by Copeland is well suited to meet the urgency of the moment with its single-screw compression technology. In 2020, we launched our subcritical CO2 single-screw platform.
Most recently, we’ve introduced the Vilter transcritical CO2 single-screw compressor, which is purpose-built for the rigors of industrial applications greater than 500 tons. Rated at up to 124 bar (1,800 psig), it simplifies industrial refrigeration and delivers unparalleled reliability in typical heavy-duty conditions.
Combined, subcritical and transcritical CO2 single-screw compressors offer industrial refrigeration solutions for applications from -55 to 45 °F. Designed for single- and two-stage configurations, these compressors meet the industrial market needs for purpose-built CO2 reliability and application simplicity.
Vilter by Copeland is committed to the advancement of industrial CO2 refrigeration. We’re applying Copeland’s stewardship, successes and experiential expertise in commercial CO2 refrigeration to lead the wave of CO2 use in industrial markets.
Today, we’re working with system designers, contractors and industry partners to simplify the adoption of industrial CO2 refrigeration via our subcritical and transcritical CO2 single-screw compressors. To learn more about our CO2 single-screw compression solutions, please visit our website.
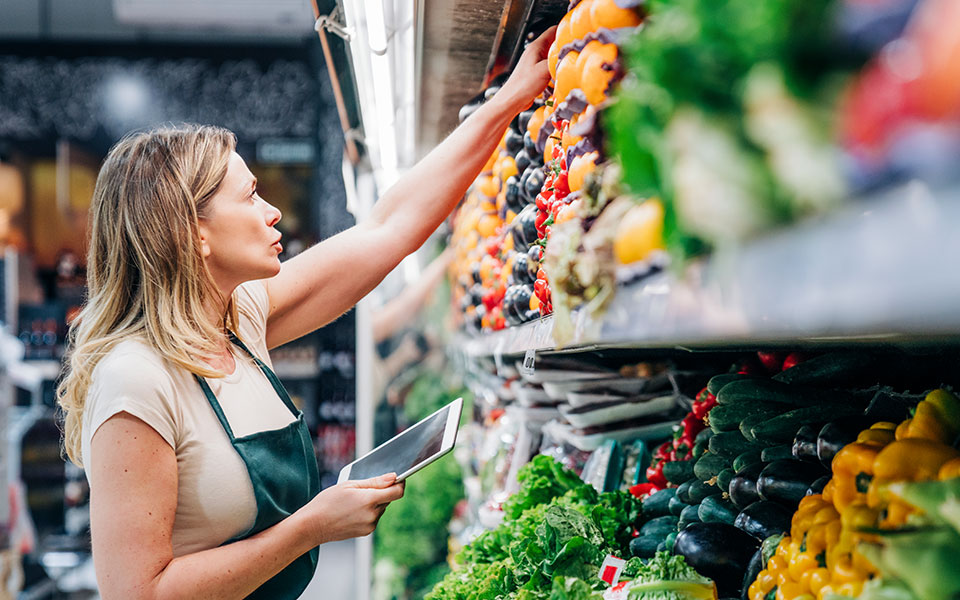
8 proven strategies for rigorous cold chain management
Preparing for the approval and safe use of A2Ls in commercial refrigeration applications...
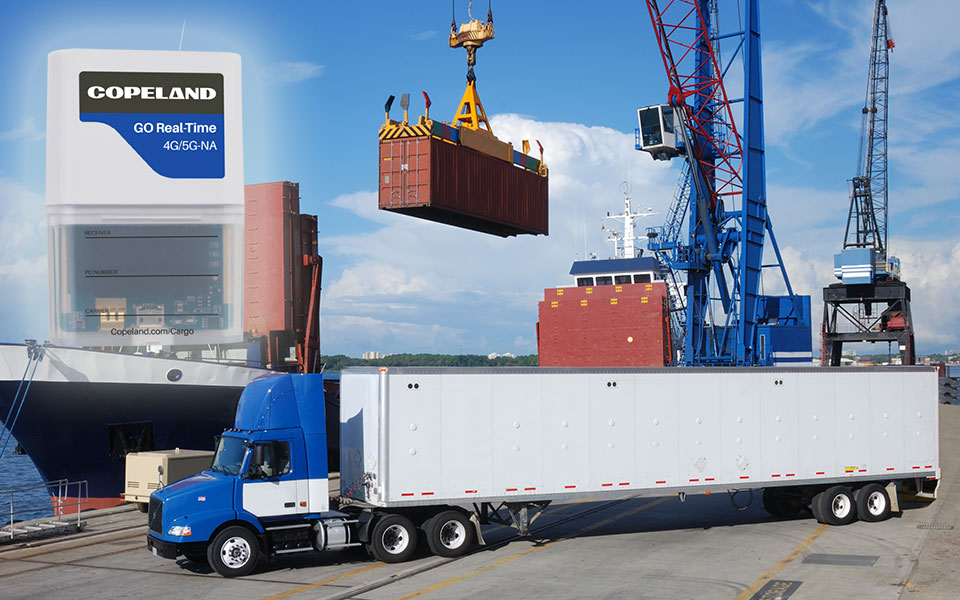
Protection for high-value shipments just got even better
We’re excited to announce the release of Copeland’s newest real-time tracker, the GO Real-Time...
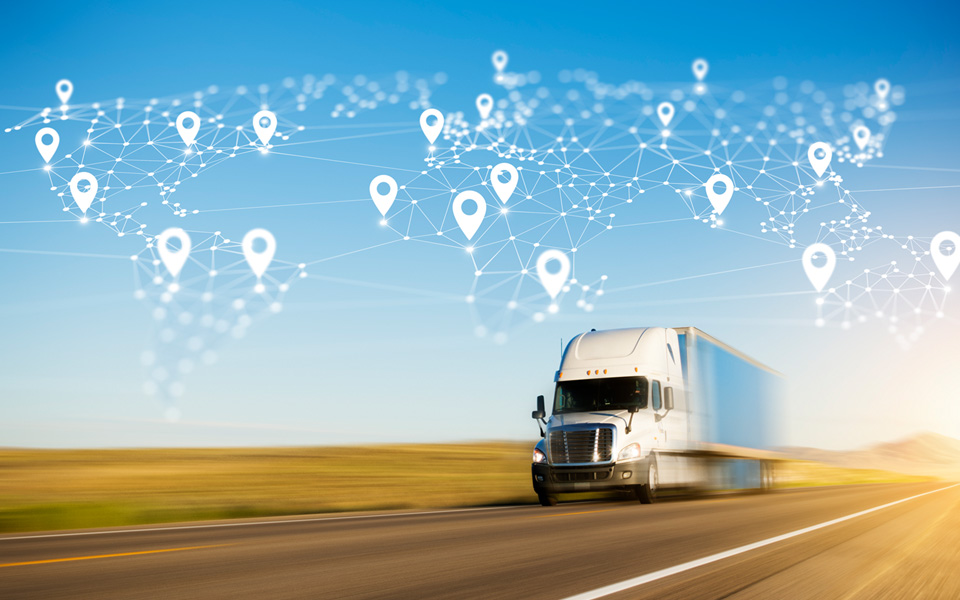
Three proven strategies to prevent cargo theft
The over-the-road (OTR) transport industry is experiencing a surge in cargo thefts. As thieves...