*On June 1, 2023 Emerson’s Climate Technologies business became a new standalone company – Copeland. Though our name has changed, we are building on more than a century of HVACR innovation and industry leadership, and Copeland continues to offer the same products, industry stewardship, and learning opportunities you’ve grown to trust. Information found on this webpage posted before June 1, 2023 may contain our old name or branding, but you can be at ease knowing it was created with the knowledge and expertise of Copeland.
With A2L refrigerants poised for regulatory approval in commercial refrigeration, many service technicians and contractors soon will be introduced to these mildly flammable alternatives. Although there are important new considerations when working with A2L refrigerants, following the basics of equipment servicing and refrigerant management will become even more essential. As part of our A2L Fundamentals video and blog series, I’ll explore the new procedures and best practices for ensuring technician safety when servicing A2L systems.
When we look at the rapidly evolving refrigerant landscape, A2L refrigerants are set to play increasingly important roles in the future of commercial refrigeration. Not only have safety standards been updated with A2L requirements, but their lower-global warming potential (GWP) ratings meet the Environmental Protection Agency’s (EPA’s) proposed 300 GWP (and below) thresholds. Achieving these lower-GWP levels results in lesser degrees of flammability than R-290, resulting in the ASHRAE “lower flammability” classification.
To date, very few A2L refrigeration systems have been installed in the U.S. It’s no surprise then that the technician community has many questions about how the emergence of A2Ls will impact their future servicing requirements.
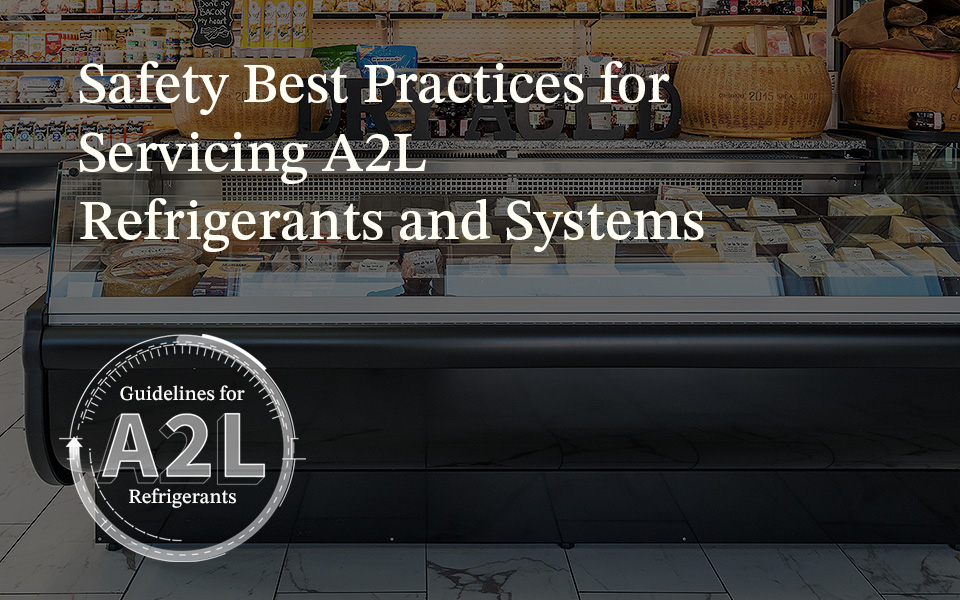
New A2L servicing requirements and tools
When servicing systems with A2L (or A3) refrigerants, technicians should familiarize themselves with new safety considerations and handling requirements. The first step is to identify which specific refrigerant is being used by looking for refrigerant labels on the system. Look for red markings on all service fittings — on the system and around compressors — and be sure to clearly mark them for the next technician who may service the system.
Similarly, A2L storage cylinders will have a red band (stripe) or the entire top painted red to indicate the presence of a flammable refrigerant. A2L tanks have a pressure relief valve that’s designed to release only enough refrigerant to reduce the pressure. In addition, to further distinguish A2L tanks from other types of refrigerants, A2L cylinders will most likely have a left-hand thread.
Next, it’s important to use specific tools that are designed and certified for use with A2Ls, such as gauges, vacuum pumps, leak detection and refrigerant recovery machines. Compared to the process of repairing A1 refrigerant-based systems, A2Ls require three mandatory steps that are already considered industry-accepted best practices:
- Purge with nitrogen.
- Evacuate the refrigerant.
- Perform leak and pressure tests.
To help ensure technician safety when servicing A2L systems, it’s important to work in a well-ventilated area and deploy a continuous leak monitoring and detection system. This may be stating the obvious, but utilizing a torch to braze connections can help ensure a safe environment before higher risk activities ensue. Generally, it’s important to be especially aware of your servicing space — including the presence of other people or potential hazards — when working on an A2L system. Over time, as A2L systems proliferate throughout retail environments, these safety procedures will become second nature.
Use only A2L-certified components
It’s important for service technicians to understand that legacy A1 refrigeration systems cannot be retrofitted for use with A2L refrigerants; further, many components used in A1 systems are simply not allowable in A2L systems. Componentry, material compatibility and a variety of other construction factors that could potentially cause a safety hazard all must be taken into consideration.
The use of A2L-certified electronic controls — such variable frequency drives, compressor electronics and case controls — is especially important to remove the potential for electrical sparking in any areas where there could be system leaks. As such, make sure that all new installations or remodels that leverage an A2L refrigerant use A2L-qualified equipment and follow all manufacturers’ guidelines.
A2L educational resources
Today, technicians can access a variety of reliable sources to learn more about servicing flammable refrigerants, including A2Ls and the A3, R-290. The Refrigeration Service Engineers Society (RSES) website offers coursework, exams and certification. They have developed best practice guidelines and other useful pieces of information to help educate the contractor workforce.
Emerson* Educational Services also offers self-paced online courses and in-person, instructor-led training. We’re committed to helping the industry transition to the next generation of lower-GWP refrigerants, including laying a foundational understanding of working with flammable refrigerants.
To learn more about safe servicing best practices, please view the A2L Fundamentals video series. Visit our A2L resource center to learn more about how Emerson* is helping the commercial refrigeration industry prepare for the emergence of A2L refrigerants.
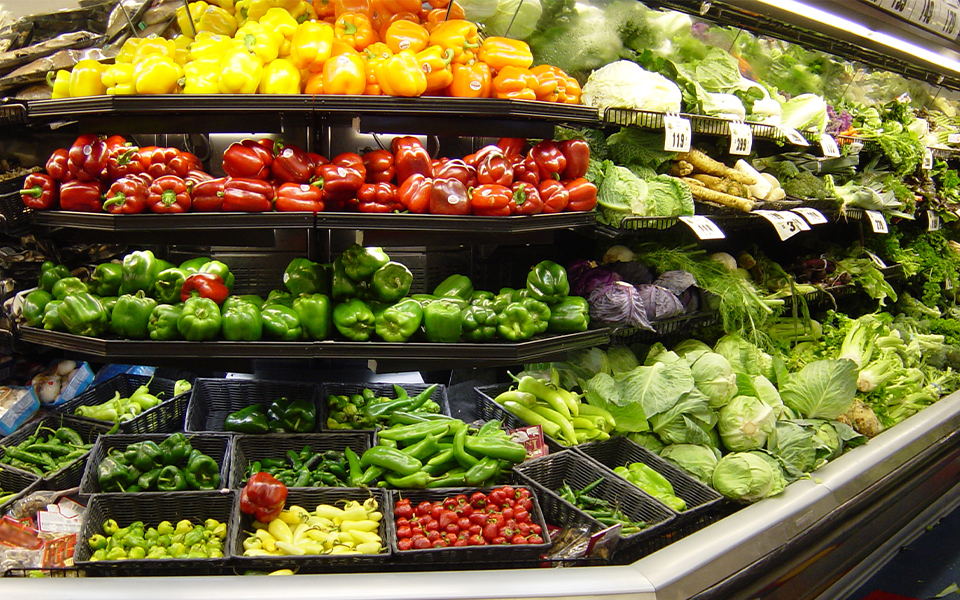
Facility Health Score Insights Program Transforms Enterprise Maintenance
Leveraging refrigeration performance data drives food retail cost reductions. Maintaining proper...
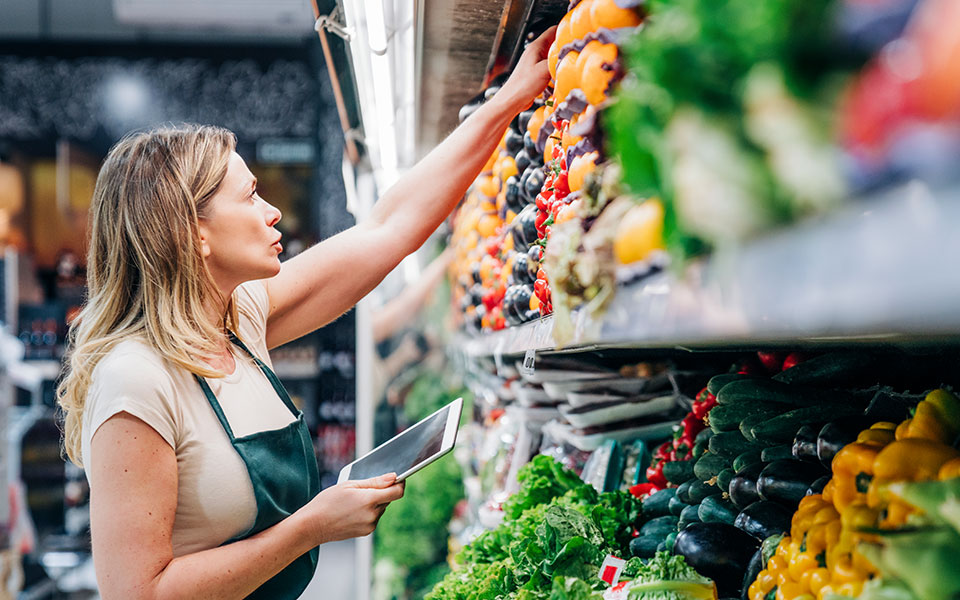
8 proven strategies for rigorous cold chain management
Preparing for the approval and safe use of A2Ls in commercial refrigeration applications...
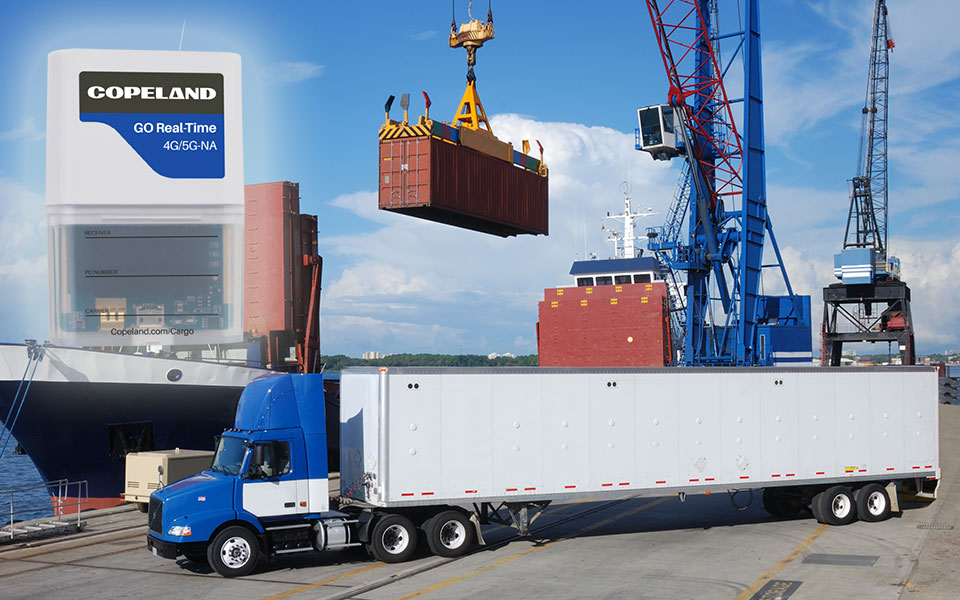
Protection for high-value shipments just got even better
We’re excited to announce the release of Copeland’s newest real-time tracker, the GO Real-Time...