*On June 1, 2023 Emerson’s Climate Technologies business became a new standalone company – Copeland. Though our name has changed, we are building on more than a century of HVACR innovation and industry leadership, and Copeland continues to offer the same products, industry stewardship, and learning opportunities you’ve grown to trust. Information found on this webpage posted before June 1, 2023 may contain our old name or branding, but you can be at ease knowing it was created with the knowledge and expertise of Copeland.
Over the past few years, supply chain disruptions have been a persistent reality for producers and shippers of perishable foods. Port and rail strikes, labor and truck driver shortages, and rising fuel costs have all taken tolls on the fresh and frozen food cold chain. Today, the tasks of maintaining quality and safety are more difficult than ever. Many stakeholders have found themselves scrambling to solve problems as they arise and always seem to be waiting for the next emergency. In a recent article for Food Logistics, I explored how data can be used to shift this reactive pattern to a more proactive — and effective — cold chain management strategy.
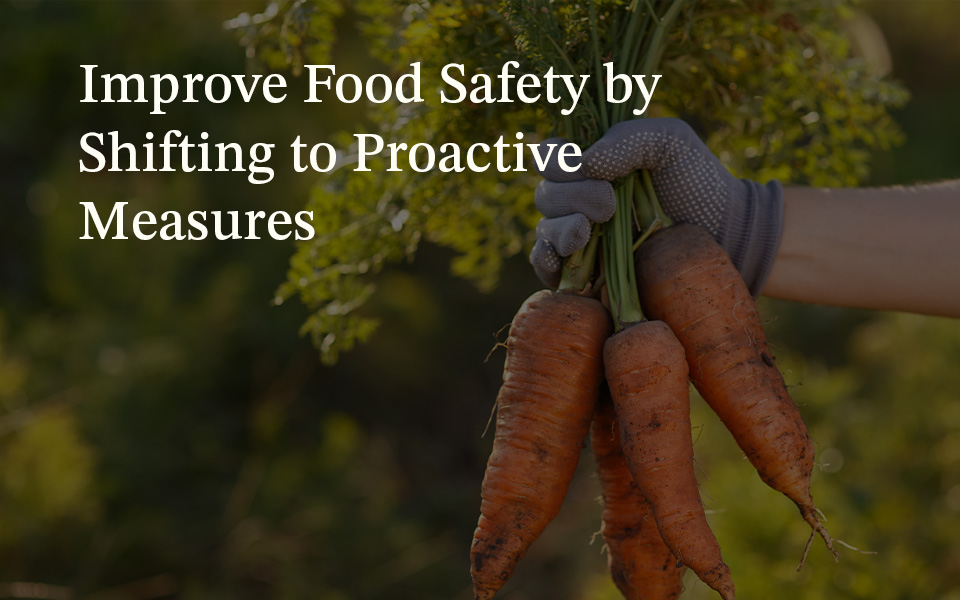
For perishable food producers and suppliers, limiting the potential for foodborne illness is the top priority in their quality control (QC) initiatives. Whether you’re shipping produce or proteins, keeping products at proper temperatures throughout every link in the cold chain is critical to preserving food safety and quality.
We know that foodborne illness outbreaks and food recalls can cause significant harm and inconvenience to consumers, but the ramifications for growers and their retail partners are often underestimated. According to a recent study by FoodLogiQ, a foodborne illness incident can tarnish producers’ reputations and increase the risks of legal, financial and regulatory penalties. Among the far-reaching consumer impacts include:
- 44 percent will avoid the brand for a few months after an outbreak
- 20 percent will never return/use the brand again
- 20 percent will return once the issue is resolved
- 16 percent will switch to a competitor’s brand
Retail partners may be even less forgiving and seek an alternate provider to mitigate future risks to their customers and operations. Regardless of the current supply chain challenges, delivering the safest and freshest products possible is fundamental to maximizing consumer safety and protecting stakeholder reputations.
Overcome trucking industry challenges
Since the onset of COVID-19, the trucking industry has been subjected to a multitude of trials — from historic spikes in food retail volumes to the harsh realities of a post-pandemic economy. A growing shortage of drivers continues to threaten supply chain stability. Many drivers who have remained must use aging trucks with sub-optimal insulation capabilities in their refrigerated trailers. These factors not only contribute to product shortages but also place new strains on the perishable cold chain.
Today, growers and shippers have access to tools and technologies that can help them to avoid issues from perishable foods that have ripened past peak quality. These solutions leverage Emerson* GO real-time temperature tracking devices and our cloud-based, data-driven Oversight cargo software to deliver real-time alerts and historic insights into cold chain performance. They can help stakeholders transition from reacting to problems after-the-fact to relying on data to prevent them from happening in the first place.
For example, stakeholders can be notified at regular intervals when shipper temperatures deviate from setpoints to help verify that a truck remains set in continuous refrigeration mode. If needed, they can take an alternate course of action before any damage to perishables can occur. And by aggregating data points from previous shipments, Oversight can reveal deeper insights and long-term trends that can inform future decisions, such as:
- Shippers or shipping lanes where temperature excursions seem to occur most frequently
- Products that are most susceptible to temperature issues
- Seasonal and geographic factors that impact reefer temperatures
- Distribution centers (DCs) that may be allowing careless cold chain management
Implement holistic cold chain management
Many leading growers and retailers are extending this proactive philosophy into every aspect of their cold chain businesses. By shifting their focus from reacting to emerging issues to implementing preventative (or pre-emptive) actions, stakeholders can maximize food safety throughout the perishable lifecycle.
For example, growers of fresh produce know that achieving cold chain safety is a process that starts from the point of harvest and continues through processing, in-transit shipping and cold storage — all before final delivery to grocers and restaurants. To reduce the risks of spoilage or contamination, producers need QC programs that shed light on temperature management challenges and support continuous improvement in handling procedures.
We provide the robust technological infrastructure to support advanced QC best practices, giving producers, shippers and retailers the visibility and insights into how perishables are handled, shipped and stored at every step of the cold chain. By using the data analytics capabilities in Oversight cargo softwarestakeholders can perform holistic cold chain management across their shipping network.
Simplify management by integrating data silos
Producers, retailers, shippers and third-party logistics (3PL) providers frequently need to work with multiple software platforms, such as an enterprise resource planning (ERP) system, a warehouse management system (WMS) and a transportation management system (TMS). When trying to investigate cold chain issues, this can create needless duplication of efforts, especially as order volumes multiply.
Many receivers mandate the use of temperature loggers and require their vendors to track information, such as purchase order numbers and the serial number of the shipper’s tracking device. These additional data fields create even more work — at a time when companies across the industry are facing historic labor constraints.
Oversight simplifies these complexities, can reduce overhead, and minimize the chances for human error. Its data integration module enables stakeholders to consolidate in-transit cold chain data into a seamless experience within their existing software platforms. This way, shipment updates and system alerts can be combined into a single view — including the option to streamline shipment creation into one system, thereby eliminating the need for multiple logins.
To learn how Oversight cargo software and value-added services can help you make the shift to proactive cold chain management, please visit our website.
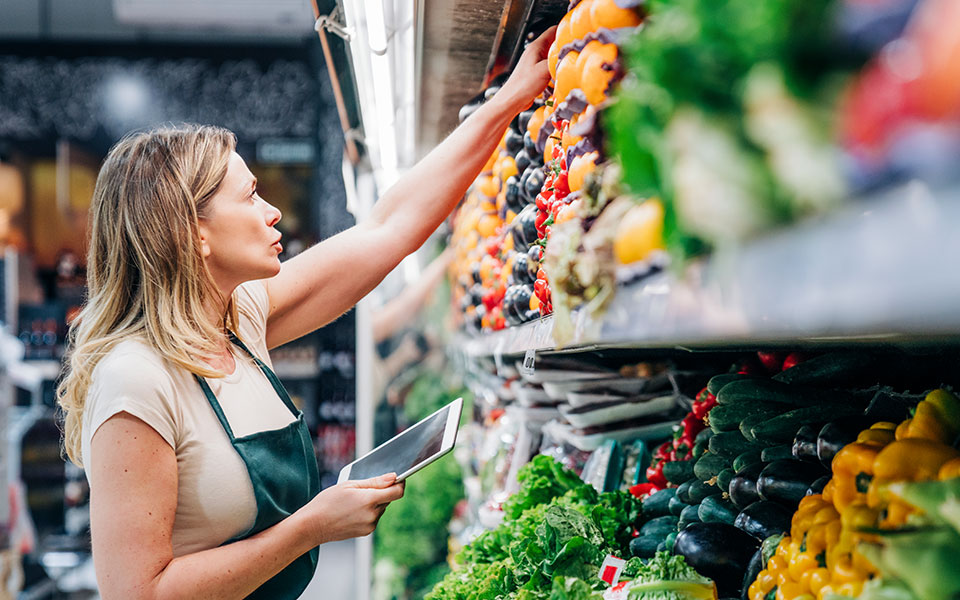
8 proven strategies for rigorous cold chain management
Preparing for the approval and safe use of A2Ls in commercial refrigeration applications...
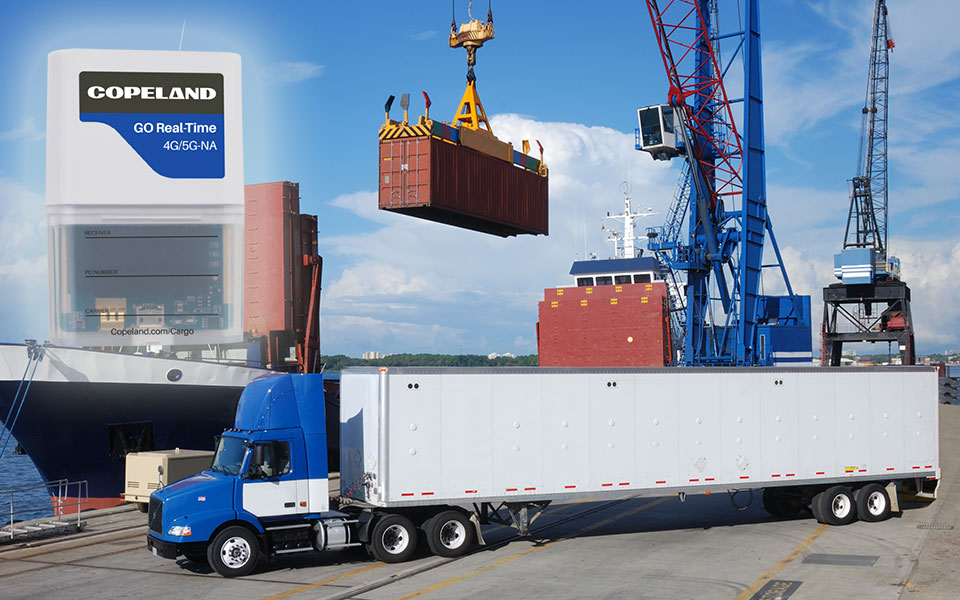
Protection for high-value shipments just got even better
We’re excited to announce the release of Copeland’s newest real-time tracker, the GO Real-Time...
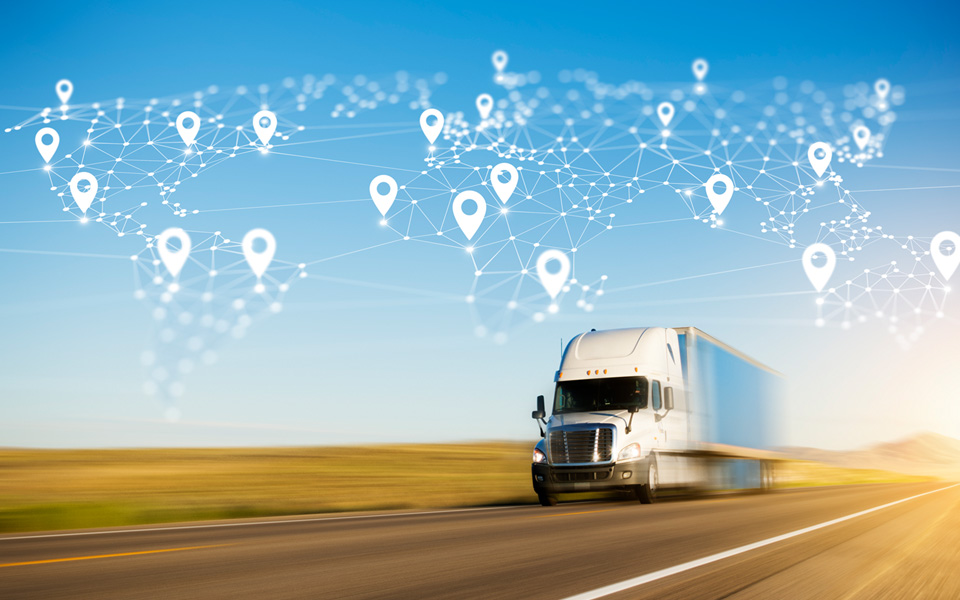
Three proven strategies to prevent cargo theft
The over-the-road (OTR) transport industry is experiencing a surge in cargo thefts. As thieves...