*On June 1, 2023 Emerson’s Climate Technologies business became a new standalone company – Copeland. Though our name has changed, we are building on more than a century of HVACR innovation and industry leadership, and Copeland continues to offer the same products, industry stewardship, and learning opportunities you’ve grown to trust. Information found on this webpage posted before June 1, 2023 may contain our old name or branding, but you can be at ease knowing it was created with the knowledge and expertise of Copeland.
Today’s c-store operators are deploying facility management control systems to meet customer demands for eco-friendly initiatives and improve energy efficiencies. This blog is based on a recent article that described how United Dairy Farmers utilizes Emerson’s Site Supervisor to achieve these goals.

Appealing to eco-conscious consumers is driving c-stores to implement more sustainable practices. From product offerings and water usage to lighting and energy consumption, c-stores are instituting numerous environmentally friendly initiatives, which are not only attracting customers but also reducing operating costs. United Dairy Farmers (UDF) has experienced the benefits of this strategy firsthand.
With nearly 200 locations in Ohio, Kentucky and Indiana, UDF’s commitment to energy efficiency has produced dividends to their bottom line. This initiative began nearly two decades ago when UDF’s engineering consulting firm, Springridge Partners, installed an Emerson control system in each store to monitor the performance of HVAC, refrigeration and lighting systems. The control systems were set up to alert UDF store managers of any operational concerns, allowing them to take fast preventative maintenance actions and avoid full system failures — thereby saving on product loss, energy and labor costs.
By creating refrigeration setpoints and alarms, store managers receive alerts when a refrigeration system is not operating properly. For example, if case temperatures exceed setpoints, the control system sends an alert to the store manager and maintenance staff, who can then dispatch the appropriate personnel to fix the issue. If compressor temperatures rise or the amperage increases over a short period of time, the system sends alerts of potential compressor failure, giving managers the opportunity to proactively replace it before a downtime incident occurs.
The control system allows UDF and Springridge Partners to determine how much energy the chain is using and make necessary adjustments. One of the first efficiency initiatives they implemented was upgrading the stores’ lighting fixtures to all-LED lighting. Each upgrade of an older UDF store from T-12 florescent lighting to LED delivers nearly 75 percent savings on lighting costs. LED lighting upgrades also reduce associated maintenance and labor costs because lights don’t have to be changed nearly as often.
Recently, UDF upgraded to Emerson’s new Site Supervisor facility control platform in its newest store location in Sharonville, Ohio. This upgrade allows UDF to remotely view the store’s energy usage and investigate consumption variances in real time. Technicians can simply log in to see what’s happening at the store, and then talk to the store manager to decide whether they need a service call. This process also allows employees to make the best use of their time instead of responding to a false alarm.
“The new Emerson Site Supervisor is a continuation of our strategy to integrate technology into our operations. This particular technology will allow our team to be more proactive in addressing issues before they become emergencies, and it allows us to maintain the quality of our products at a very high level,” said Brad Lindner, UDF’s CEO.
What’s more, the system is expected to assist UDF in its plans to implement further reductions in energy usage across its operations.
“By allowing our team to analyze the trend data, we are able to make intelligent decisions regarding setpoints, equipment selections and food quality. We will continue to look for new ways to leverage technology in other areas of our business to increase both awareness and engagement of our staff as a whole,” Lindner said.
Learn more about Site Supervisor and its capabilities to see how it can drive energy efficiency in your operations.
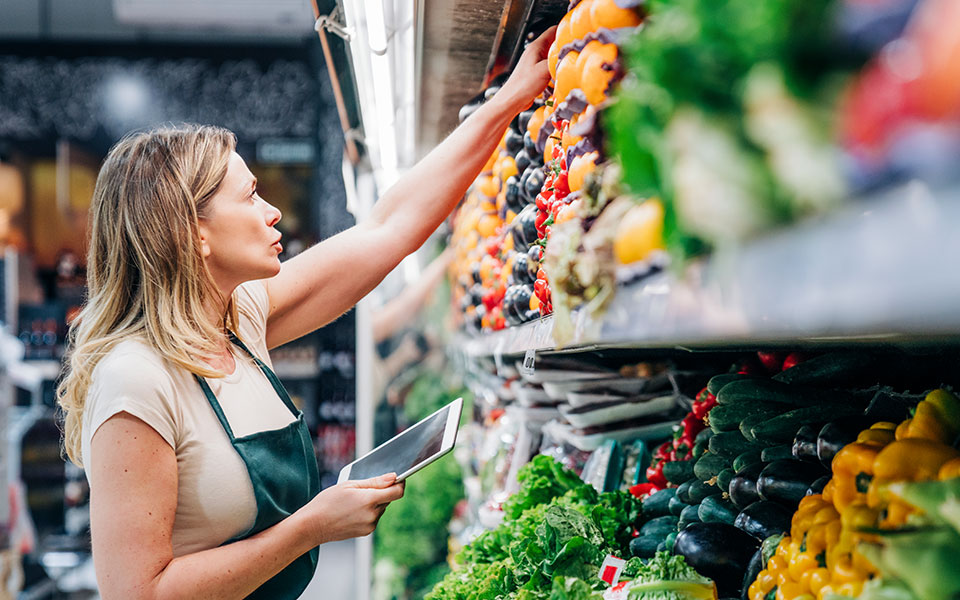
8 proven strategies for rigorous cold chain management
Preparing for the approval and safe use of A2Ls in commercial refrigeration applications...
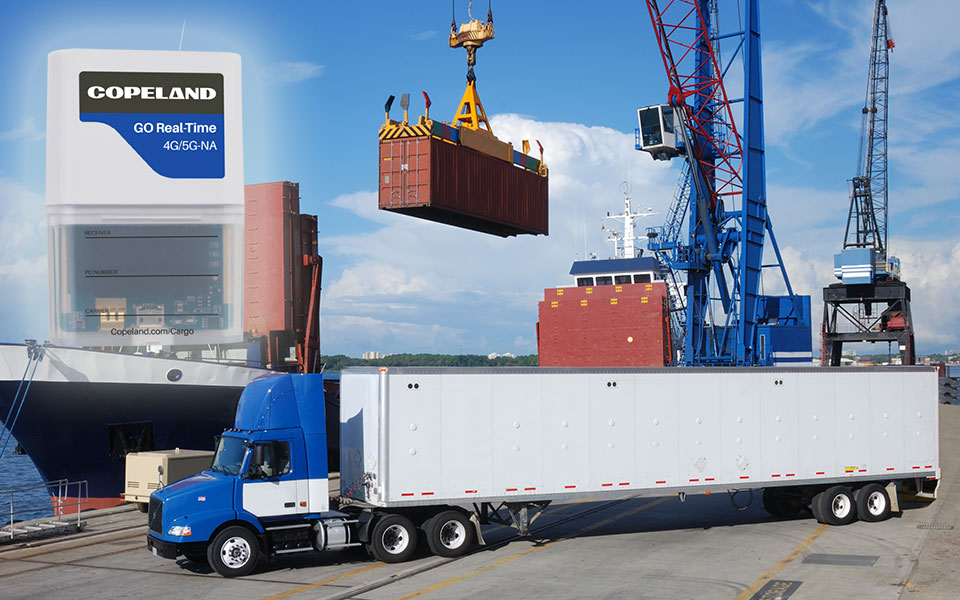
Protection for high-value shipments just got even better
We’re excited to announce the release of Copeland’s newest real-time tracker, the GO Real-Time...
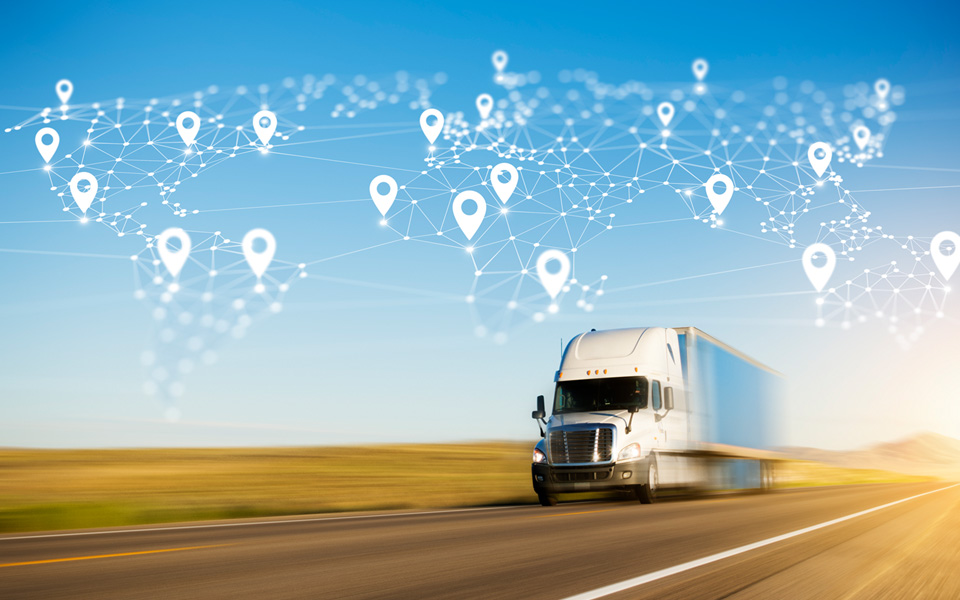
Three proven strategies to prevent cargo theft
The over-the-road (OTR) transport industry is experiencing a surge in cargo thefts. As thieves...