*On June 1, 2023 Emerson’s Climate Technologies business became a new standalone company – Copeland. Though our name has changed, we are building on more than a century of HVACR innovation and industry leadership, and Copeland continues to offer the same products, industry stewardship, and learning opportunities you’ve grown to trust. Information found on this webpage posted before June 1, 2023 may contain our old name or branding, but you can be at ease knowing it was created with the knowledge and expertise of Copeland.
After years of uncertainty for supermarket retailers, the transition to lower-global warming potential (GWP) refrigerants is underway. The regulatory wheels driving the phasedown of hydrofluorocarbon (HFC) refrigerants are in motion, and it’s crunch time for retailers who face critical decisions about their future refrigeration strategies. I recently contributed an article for Chain Store Age that explored key factors in evaluating the total cost of ownership (TCO) equation.
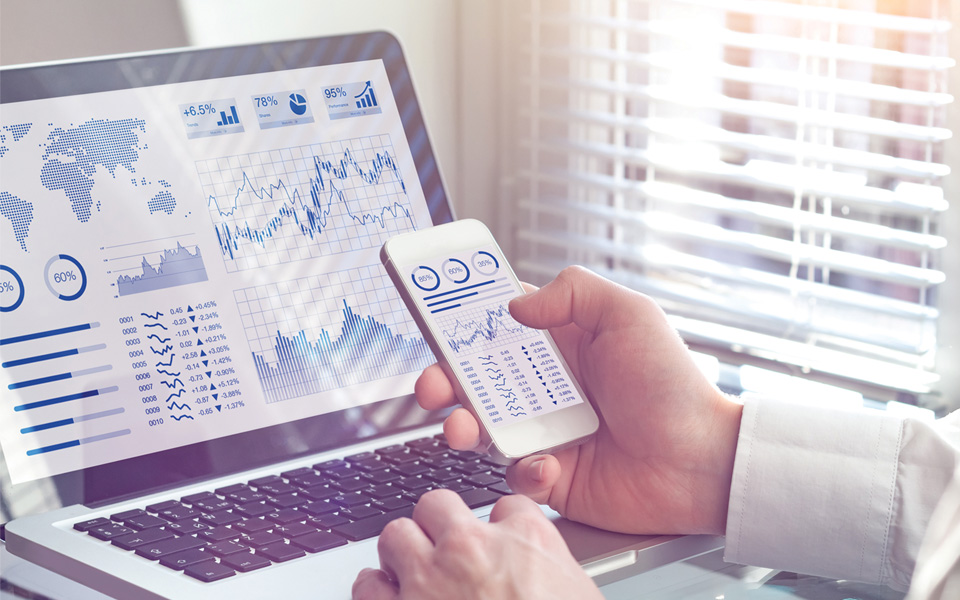
Recently, the Environmental Protection Agency (EPA) introduced proposals that support the phase-in of lower-GWP refrigerant alternatives. Its Technology Transition proposal would enforce sector-based GWP limits of 150 and 300 in new commercial refrigeration equipment beginning in 2025, while its SNAP Rule 26 proposal would approve the use of lower-flammability A2L refrigerants in these applications.
At the same time, many retailers are in various stages of their sustainability journeys, implementing initiatives to lower their carbon footprints and work toward Net Zero targets. All these efforts are driving fundamental changes to refrigeration equipment technologies and system architectures — in both new store installations and systems retrofits.
For supermarket retailers, equipment and/or refrigerant decisions need to align with their operational preferences, sustainability goals and financial budgets. To help retailers make best-fit equipment decisions, Copeland has conducted extensive research on the costs to operate next-generation refrigeration technologies throughout the lifecycle. The following are five key considerations for evaluating the TCO of your future refrigeration investments.
1. CapEx vs. OpEx — Understanding TCO starts with differentiating between first and ongoing costs. Capital expenditures (CapEx) refers to first costs of equipment investments and the costs of installation, which are dependent on the type of equipment and relative complexity of the installation. Operating expenses (OpEx) include the costs to operate and maintain the equipment throughout the system lifecycle. Since retailers typically utilize commercial refrigeration equipment for up to 15–20 years, it’s essential to take a long-term view of OpEx.
2. Local energy rates and peak demand charges — Some utilities offer demand response programs and opportunities for grid interactivity, which can provide incentives to offset first costs and install energy-efficient equipment. Typically, this requires deploying a measurement and verification (M&V) system to track energy consumption and enable grid interactive building (GIB) capabilities, which can help retailers to avoid incurring peak energy charges.
3. Carbon intensity profile — Evaluating the carbon intensity of selected equipment requires considering the total equivalent warming impact (TEWI) of the system’s energy consumption and refrigerant GWP. To lower their carbon footprints, many retailers are leveraging heat reclaim for store resource needs (water and/or air heating, etc.). Others are looking for opportunities to offset energy costs or manage sustainability goals by selling or purchasing carbon credits.
4. Natural resource availability and costs — Water is an essential resource for water-assisted (adiabatic) systems, such as a CO2 transcritical booster with an adiabatic gas cooler, or an R-290 micro-distributed system with a chilled water loop. If water is vital to supporting a particular equipment strategy, retailers will have to evaluate this need per each installation location.
5. Trained service technicians — Technicians are on the front lines of the refrigerant transition. Successful implementation of emerging lower-GWP architectures can require new training or education. The availability and skill levels of regional service technicians are essential TCO considerations when devising next-generation refrigeration strategies. Although many technicians are being trained and prepped for this transition, their skill levels with a particular refrigerant (e.g., CO2) may differ from region to region. Accessing these skills may impact the costs to secure their services.
Copeland is committed to helping retailers select refrigeration architectures that align with their operational preferences and lower their TCO throughout the system lifecycle. We recently completed a comprehensive TCO study that evaluates the relative CapEx and OpEx of emerging refrigeration architectures. To speak with our TCO experts and review the many insights within this report, please contact your Copeland representative.
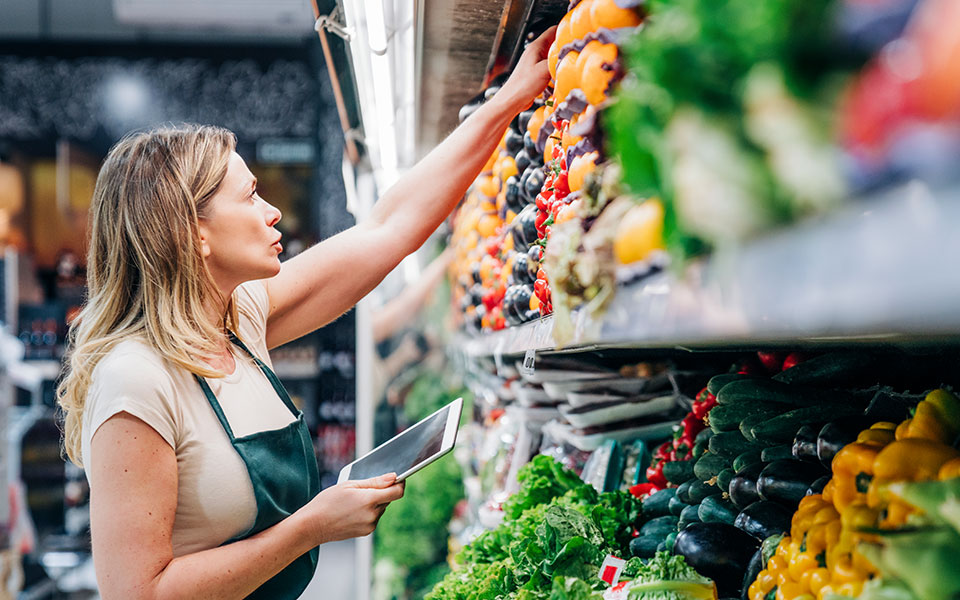
8 proven strategies for rigorous cold chain management
Preparing for the approval and safe use of A2Ls in commercial refrigeration applications...
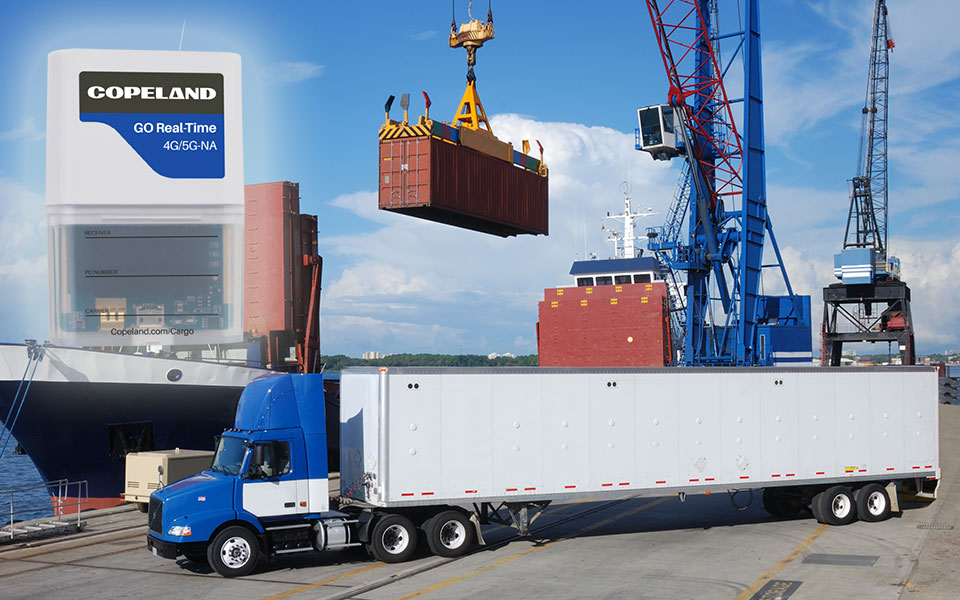
Protection for high-value shipments just got even better
We’re excited to announce the release of Copeland’s newest real-time tracker, the GO Real-Time...
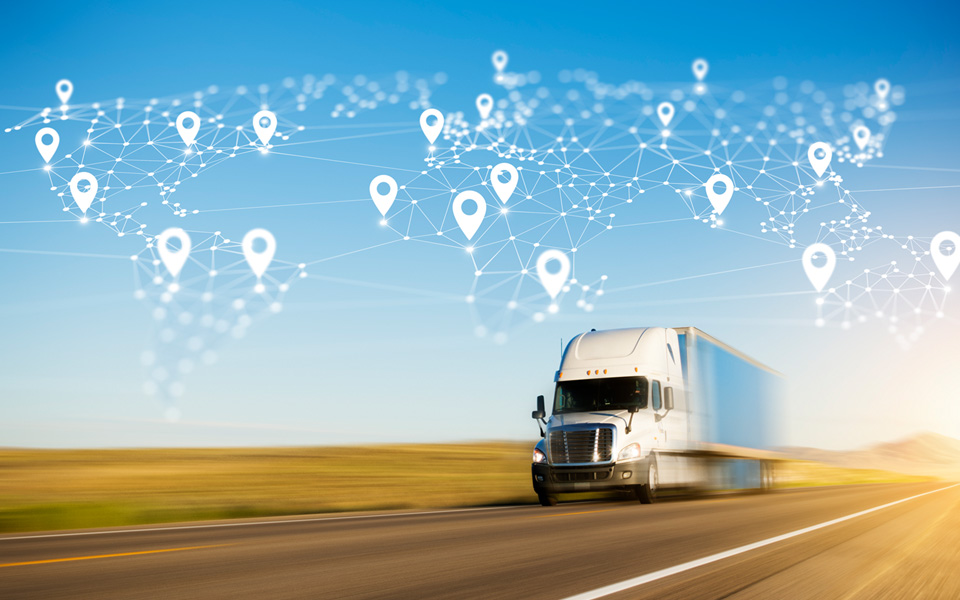
Three proven strategies to prevent cargo theft
The over-the-road (OTR) transport industry is experiencing a surge in cargo thefts. As thieves...