*On June 1, 2023 Emerson’s Climate Technologies business became a new standalone company – Copeland. Though our name has changed, we are building on more than a century of HVACR innovation and industry leadership, and Copeland continues to offer the same products, industry stewardship, and learning opportunities you’ve grown to trust. Information found on this webpage posted before June 1, 2023 may contain our old name or branding, but you can be at ease knowing it was created with the knowledge and expertise of Copeland.
From supermarkets and restaurants to cold storage and processing plants, walk-in coolers and freezers (WICFs) are designed to support a wide range of commercial and industrial uses. Because of this application diversity, it’s important to select remote condensing units (CUs) capable of delivering the required refrigeration load, system reliability, and optimum energy efficiency. In a recent article for Contracting Business, Copeland’s WICF experts examined the factors HVACR contractors should consider when sizing and selecting a CU for your application. To view the full article, click here.

Sizing and selecting a CU for a WICF application requires an understanding of multiple factors that can impact the refrigeration load, including:
- WICF construction and insulation envelopes
- Environmental conditions
- Application-specific considerations
Federal legislation has established guidelines for WICF construction and mandates for energy-efficiency standards:
- Federal Energy Independence and Security Act of 2007 — designates WICF construction guidelines for air infiltration, insulation R-values (i.e., insulation ratings), evaporator and condenser fan motor standards, lighting and more
- Department of Energy’s (DOE) Annual Walk-in Energy Factor (AWEF) — establishes minimum energy- efficiency standards for several WICF equipment classes below the 3,000 square foot limit that must meet or exceed the minimum AWEF ratings based on capacity and application (e.g., medium- [MT] or low-temperature [LT], indoor or outdoor)
Heat transmission
WICFs can experience varying amounts of heat transmission (or gain) through walls, floors, doors and ceilings. This is dependent upon construction type, insulation thickness, area exposed to ambient temperatures, and the temperature difference between the refrigerated space and the ambient air. Manufacturers of WICF panels, doors and floors typically publish R-values to help contractors calculate the refrigeration load.
When determining the ambient temperature’s impact on equipment sizing, choosing the hottest possible temperature for a given region is not a recommended design strategy. Because high ambient temperatures may occur for short durations, they may account for only a small fraction of total annual hours. Thus, selecting a target peak demand design condition should be based on a percentage of the hours exceeding a reasonable maximum temperature range during a typical summer season.
Air infiltration
Air infiltration refers to the ingress of outside air entering the refrigerated space. System designers and HVACR contractors should calculate the amount of air infiltration and its potential impacts upon the WICF refrigeration load. When outside air is introduced, the CU must be able to pull down the WICF temperature to its designated setpoint, thus increasing the refrigeration load. If the air’s moisture content is higher than the refrigerated space, its condensation will add to this load by causing latent heat. Considering all variables is essential to successfully calculating the additional heat gain due to air infiltration.
Door curtains, automatic door closers and proper door gasket maintenance can help to minimize air infiltration. It’s also important for contractors to install the evaporator unit cooler in a location that reduces the likelihood of it blowing chilled air out the door.
Product load
The product load refers to the heat gain that occurs when a product enters the WICF at a higher temperature than the storage setpoint. The resultant chilling or freezing process necessary to pull down product temperatures increases product load, as can the heat of respiration of perishable products. Total product load is the sum of these various factors.
Special applications, such as long-term perishable fruit apple storage, require more precise product load calculations. Perishable commodities have ideal cold storage temperatures and relative humidity to preserve freshness, quality and storage life. See Tables 13 and 14 in the Copeland™ Refrigeration Manual (AE 103) for recommended storage conditions of various perishables, including cut flowers and nursery stock.
Supplemental load
In addition to heat transmission, air infiltration and product load, heat gain from other sources must be factored into the total WICF cooling load estimate, including:
- Lighting
- Fan/blower motors
- Employee foot traffic (open doors and/or body heat)
- Fork trucks (loading/unloading)
The impacts of foot traffic and fork trucks are especially important in larger cold storage warehouses, frozen food plants, loading docks, click-and-collect operations, or any environment with heavy walk-in or drive-in traffic.
Selecting a CU for your WICF
Once you have determined the total refrigeration load, required evaporating temperature and expected condensing temperature, you’re ready to select a CU for your WICF application. Refrigeration equipment selection is based upon refrigeration capacity and/or the expected compressor operating time and the requirements of the defrost system.
Refrigeration load is calculated on a 24-hour basis; hourly compressor capacity is determined by dividing the 24-hour load by the desired hours of compressor operation during a 24-hour period. Important note: contractors should account for a reasonable safety factor to enable the unit to recover rapidly after a temperature rise and allow for heavier loads than the original estimate. It’s considered prudent to add a 5 to 10 percent safety factor to refrigeration load calculations.
Defrost cycles can have significant impacts on compressor capacity, because they require stopping the compressor and allowing the return air to melt the ice from the evaporator coil. When refrigerant evaporating temperature will not fall below 30 °F, frost will not accumulate on the evaporator. In these no-defrost conditions, it is considered a best practice to choose the compressor based on an 18- to- 20-hour operation.
Defrost cycles are recommended for applications with storage temperatures of 35 °F or higher and refrigerant temperatures low enough to cause frosting. In this case, contractors should select a compressor for 16 to 18 hours of operation. You can also expect to employ a defrost cycle on LT freezer applications, where 18-hour compressor operation is usually acceptable.
Copeland has developed a Box Load Calculator tool specifically to help contractors and system designers with the processes of sizing and selecting CUs for their WICF applications. Simply enter the WICF application parameters to calculate your refrigeration load and review the available CU equipment options.
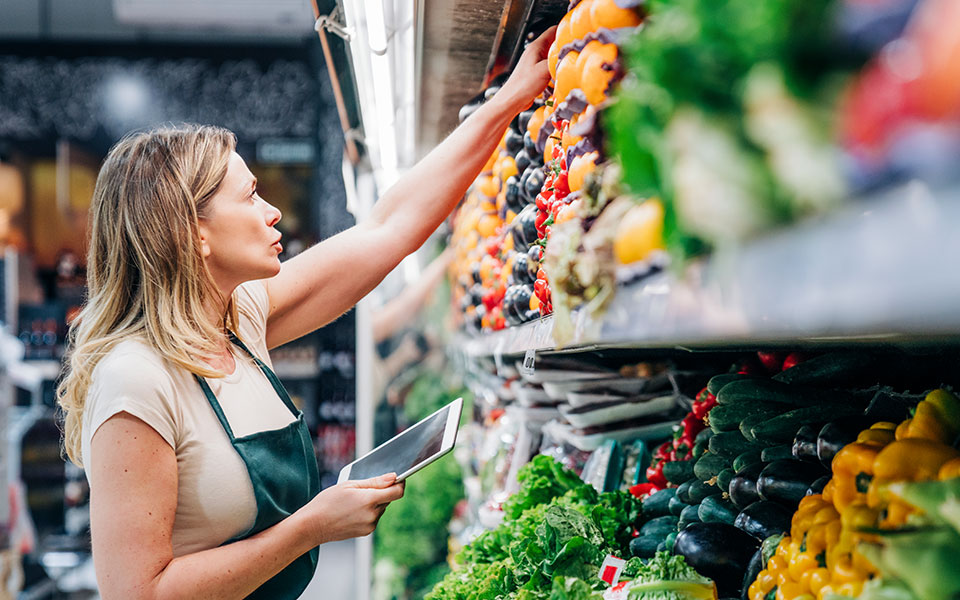
8 proven strategies for rigorous cold chain management
Preparing for the approval and safe use of A2Ls in commercial refrigeration applications...
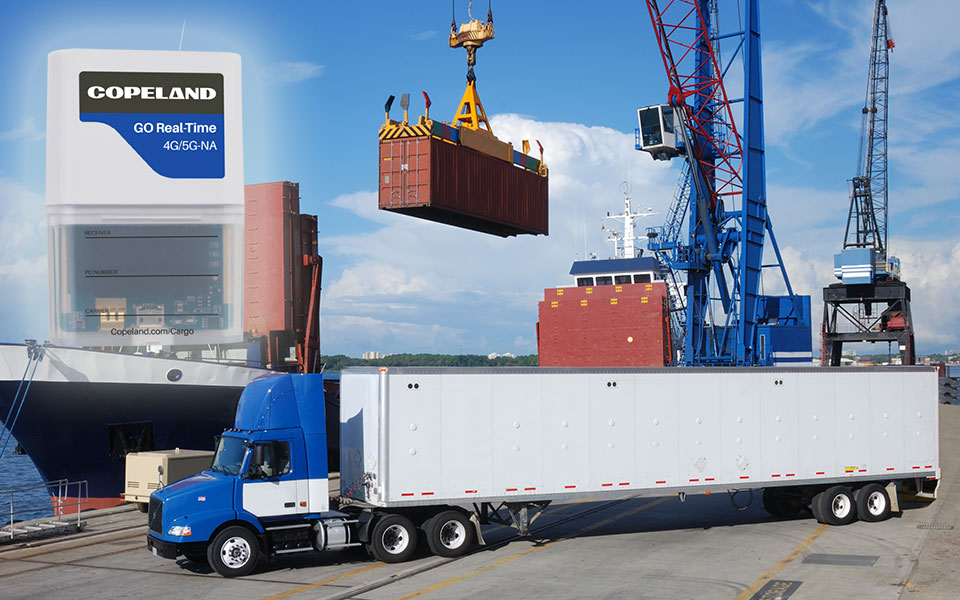
Protection for high-value shipments just got even better
We’re excited to announce the release of Copeland’s newest real-time tracker, the GO Real-Time...
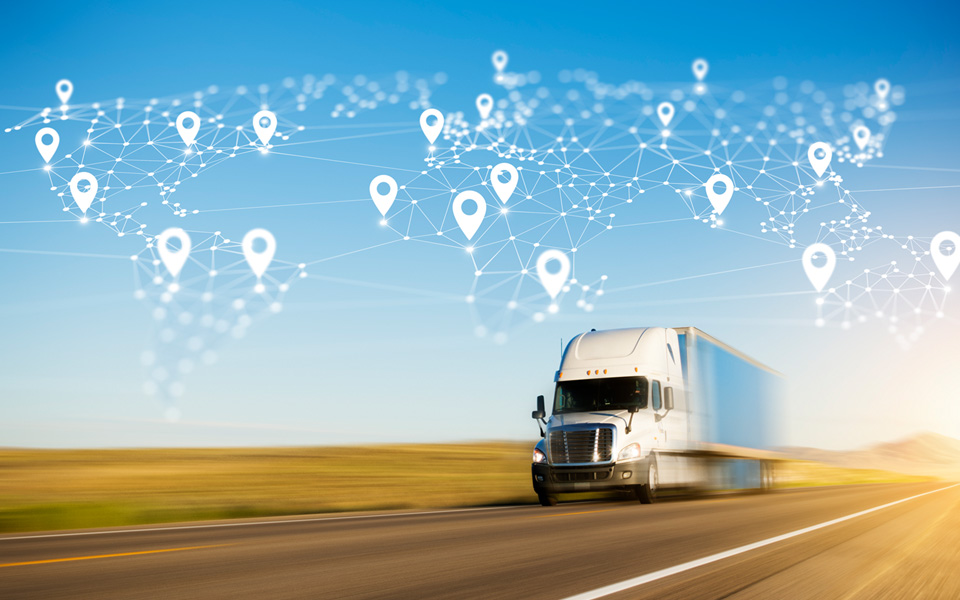
Three proven strategies to prevent cargo theft
The over-the-road (OTR) transport industry is experiencing a surge in cargo thefts. As thieves...