*On June 1, 2023 Emerson’s Climate Technologies business became a new standalone company – Copeland. Though our name has changed, we are building on more than a century of HVACR innovation and industry leadership, and Copeland continues to offer the same products, industry stewardship, and learning opportunities you’ve grown to trust. Information found on this webpage posted before June 1, 2023 may contain our old name or branding, but you can be at ease knowing it was created with the knowledge and expertise of Copeland.
With its excellent thermodynamic properties and high efficiencies, ammonia (aka NH3; refrigerant name R-717) has long been the preferred refrigerant in low-temperature (LT) cold storage warehouses and light-industrial refrigeration applications. But because operators assume a degree of risk when using ammonia, many are evaluating the potential of CO2 (refrigerant name R-744) as a green, lower-risk alternative. In a recent article for Engineered Systems, I explored the emergence of CO2 in the industrial sector.
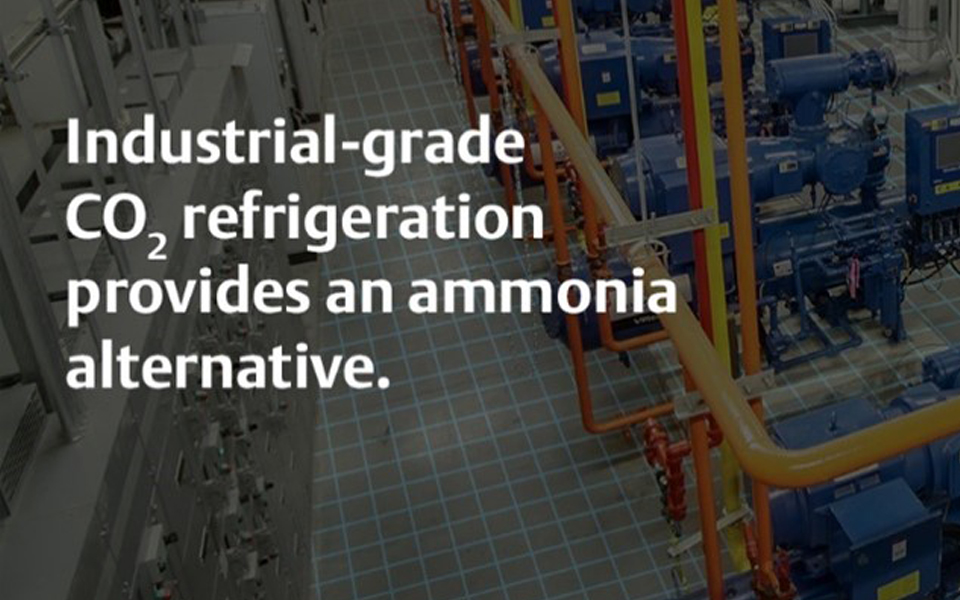
Despite increasing global adoption in commercial refrigeration, CO2 has yet to make significant inroads in the industrial sector. Its high operating pressure and unique characteristics pose equipment design and system architectural challenges for original equipment manufacturers (OEMs). But today’s industrial OEMs are building upon the framework of successful CO2 architectures used within food retail applications, such as CO2 transcritcal booster and cascade systems. Theoretically, it’s a matter of scaling these systems up for industrial use.
Market drivers of CO2 adoption
Efforts to increase the supply of CO2-based industrial refrigeration equipment are driven largely by new market demands.
-
- Last-mile delivery considerations — In response to the accelerated adoption of e-commerce in food retail applications, many light-industrial distribution and fulfillment (D&F) facilities have arisen in urban areas to shorten the distance to consumers. But the risk of an ammonia leak in highly populated areas threatens to not only shut down a facility, but also evacuate the surrounding area. Operators of these light-industrial facilities are seeking a lower-risk, green alternative.
- Lowering ammonia charges and designing for safety — The Occupational Safety and Health Administration (OSHA) has mandated safety requirements for systems charged with more than 10,000 pounds of ammonia. This has led to the exploration of all-CO2system architectures and those that combine CO2 and ammonia to lower ammonia charges and move refrigeration circuits out of occupied spaces.
- Global hydrofluorocarbon (HFC) refrigerant phasedown — The recent passing of the American Innovation and Manufacturing (AIM) Act has brought the global HFC phasedown back into focus in the U.S. Meanwhile, the California Air Resources Board (CARB) and/or U.S. Climate Alliance states are pushing forward with their own aggressive phasedown schedules. Industrial operators who have traditionally preferred using HFCs over ammonia are evaluating alternative refrigerant options, such as CO2.
- Blurring of lines between commercial and industrial OEMs — With CO2emerging in the industrial sector, and low-charge ammonia systems being trialed in commercial architectures, OEMs are leveraging their legacy experience to cross into adjacent markets. However, commercial OEMs need to understand the increased demands of industrial applications and develop equipment that is built to withstand their rigors.
- Sustainability initiatives — Regardless of all other market and regulatory considerations, many companies today are establishing and adhering to corporate sustainability objectives. This requires selecting refrigeration architectures that are both safe and environmentally friendly. As a green natural refrigerant, CO2is helping businesses to achieve these objectives.
Supporting the transition to CO2
Although it’s unlikely that CO2 will ever completely replace ammonia as the preferred refrigerant in large-charge industrial applications, CO2-based refrigeration equipment is becoming a more viable option in light-industrial scenarios.
With extensive expertise in both ammonia- and CO2-based refrigeration, Emerson is uniquely qualified to support traditional and emerging industrial applications. Our Vilter™ single-screw compression technology is not only built to withstand the rigors of industrial refrigeration, but it’s also capable of managing the high pressures of CO2 transcritical booster applications. In addition, our ever-expanding CO2 product portfolio includes a breadth of solutions for transcritical, cascade and secondary architectures.
From compression technologies, controls and variable-speed drives to supervisory services and a wide range of CO2-approved system components, we are a CO2 refrigeration solution provider and partner to leading industrial operators and food retailers.
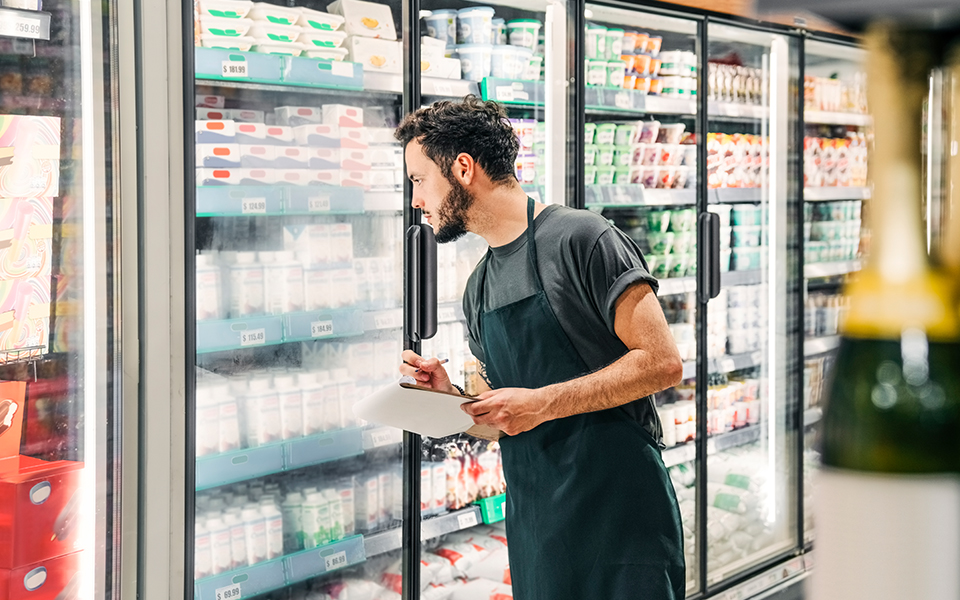
Electrical component considerations for A2L system safety
Electrical component considerations for A2L system safety As a new refrigerant category in the...
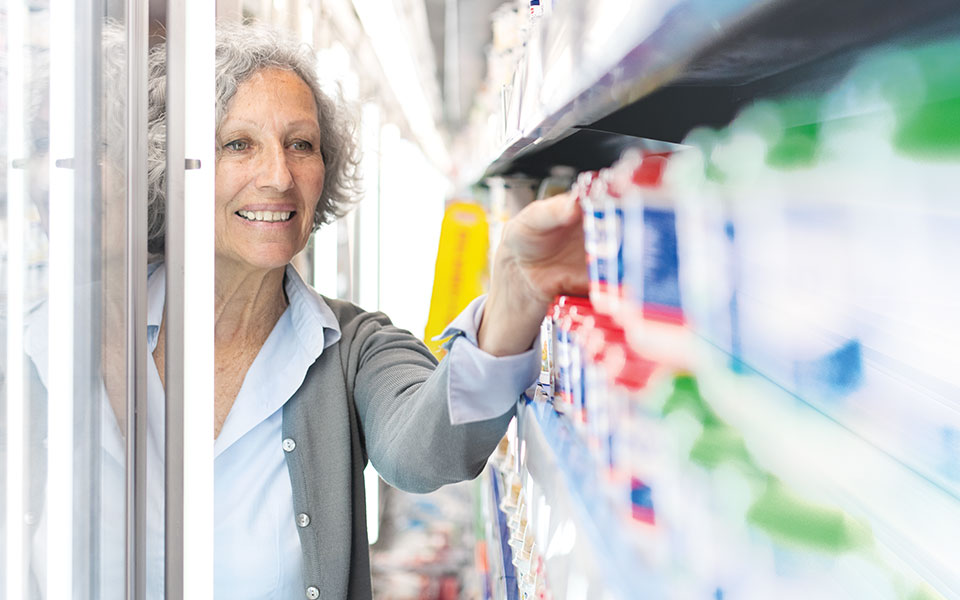
A2L refrigerant regulation updates: what you need to know today
Preparing for the approval and safe use of A2Ls in commercial refrigeration applications The move...
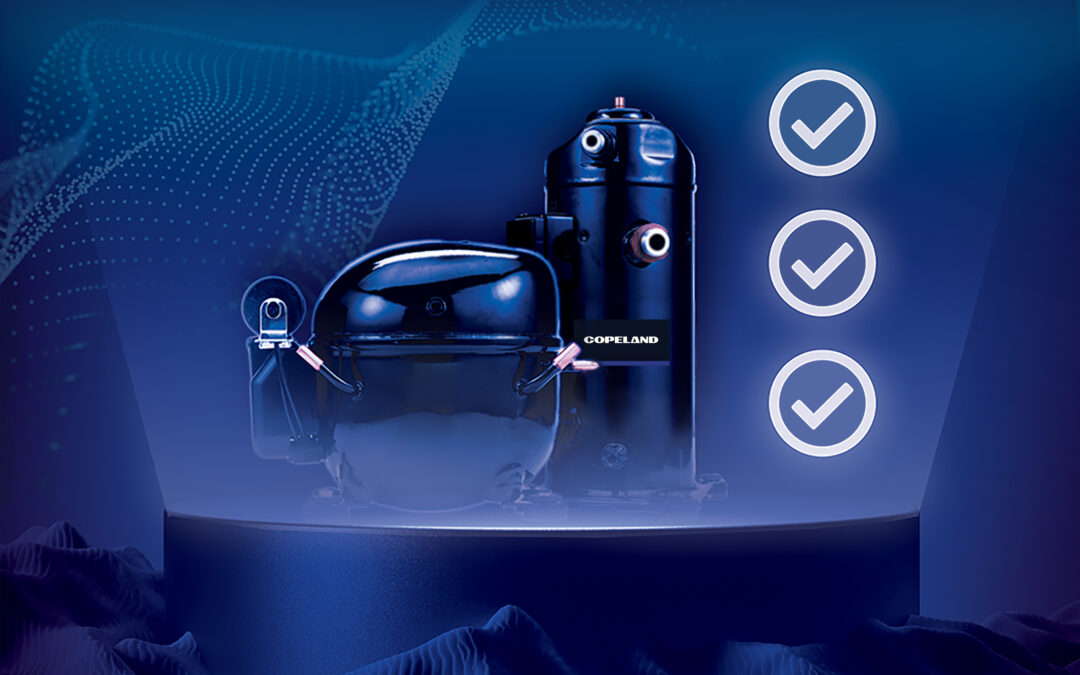
Address Efficiency Mandates with Compression Technologies
Strategies for complying with DOE and ENERGY STAR® in self-contained and remote condensing units...