*On June 1, 2023 Emerson’s Climate Technologies business became a new standalone company – Copeland. Though our name has changed, we are building on more than a century of HVACR innovation and industry leadership, and Copeland continues to offer the same products, industry stewardship, and learning opportunities you’ve grown to trust. Information found on this webpage posted before June 1, 2023 may contain our old name or branding, but you can be at ease knowing it was created with the knowledge and expertise of Copeland.
Every year on April 22, nations around the globe pause to recognize Earth Day and reflect on the importance of preserving the planet’s environment. This year will mark the 50th anniversary of the annual Earth Day commemoration; its theme is “climate action”. According to the organization’s website, “Climate change represents the biggest challenge to the future of humanity and the life-support systems that make our world inhabitable.” Thus, action is essential for mitigating the damaging impacts of climate change.

For decades, the commercial refrigeration industry has taken a global focus on climate action. In 1987, the Montreal Protocol set out to ban the use of refrigerants with ozone depletion potential (ODP) — and as of today, these efforts have proved extremely effective. But in 2020, our industry has a new environmental mandate: to phase down the use of hydrofluorocarbon (HFC) refrigerants with high global warming potential (GWP). The Kigali Amendment to the Montreal Protocol was enacted to do just that; since 2019, 20 countries are participating in these measures. At the same time, other countries have adopted their own HFC phase-down regulations, and states like California are leading the charge here in the United States.
But while the environmental focus is often on refrigerants, it’s important to understand that refrigeration must be evaluated from its total equivalent warming impact (TEWI), which considers both the impacts of refrigerants and the energy efficiency of a system throughout the lifecycle. For decades, Emerson has been committed to promoting sustainable and environmentally friendly refrigeration. Here are five best practices that we promote to achieve greener refrigeration strategies.
- Recommission your refrigeration system.Over time, refrigeration systems can drift steadily from their original commissioned performance baselines. It’s important to make sure systems are operating as efficiently as possible before considering any upgrades such as replacing a compressor. Recommissioning returns the system back to its original operating parameters and establishes a necessary baseline from which ongoing improvements can be made.
- Implement an energy measurement and verification (M&V) program.The decision to upgrade or replace a compressor must be evaluated from a holistic assessment of the refrigeration system. To gain deeper insights into system performance, we recommend implementing a formal measurement and verification program in tandem with the recommissioning process. An M&V program helps to identify holistic system energy-efficiency data and evaluate individual compressor performance, which operators can use to potentially qualify for an energy incentive program. Participating utilities may offer rebates for replacing inefficient equipment with newer, energy-efficient models.
- Retrofit to variable-capacity modulation.After identifying the low- and medium-temperature compressors that are underperforming, the next step would be to upgrade them to enable a variable-capacity compression strategy — either by upgrading to a digitally modulated compressor or adding a variable frequency drive (VFD). Replacing even one fixed-capacity compressor with a variable-capacity digital compressor can result in significant benefits, such as: improved energy efficiencies, precise matching of capacity to changing refrigeration loads, improved case temperature precision, reduced compressor cycling (on/off), and tight control over suction manifold pressures.
- Enable low-condensing operation.One often overlooked strategy — which is also factoring into some environmental regulations — is the practice of low-condensing operation (aka floating the head pressure). Instead of operating at a high fixed head pressure regardless of the ambient temperature, low-condensing operation floats the head pressure down as the ambient temperature drops — in the evening, overnight and early morning hours. This best practice utilizes electronic expansion valves (EEVs) that allow for dynamic control so that the system is no longer operating at maximum capacity during periods of cooler ambient temperatures. As a result, compressor capacity increases while wattage consumed decreases. In fact, operators can realize lower costs through energy efficiency ratio (EER) improvements of 15–20% for every 10 °F decrease in head pressure.
- Transition to lower-GWP refrigerants. Preparing for the future of refrigeration means transitioning from higher-GWP HFC refrigerants to lower-GWP alternatives. Of course, doing so will require adopting new refrigeration technologies and system architectures. From self-contained, integrated cases which utilize natural, hydrocarbon refrigerants to proven CO2transcritical booster systems and new distributed micro-booster systems that use lower-GWP refrigerants with familiar operating properties, there are a wide variety of emerging systems capable of addressing the full range of commercial refrigeration applications.
Emerson is committed to developing innovative refrigeration technologies and helping commercial refrigeration stakeholders adopt more sustainable refrigeration strategies. We’re actively developing solutions that address all the best practices listed above, and we’re working to promote future refrigeration technologies that will help our customers meet their unique sustainability goals.
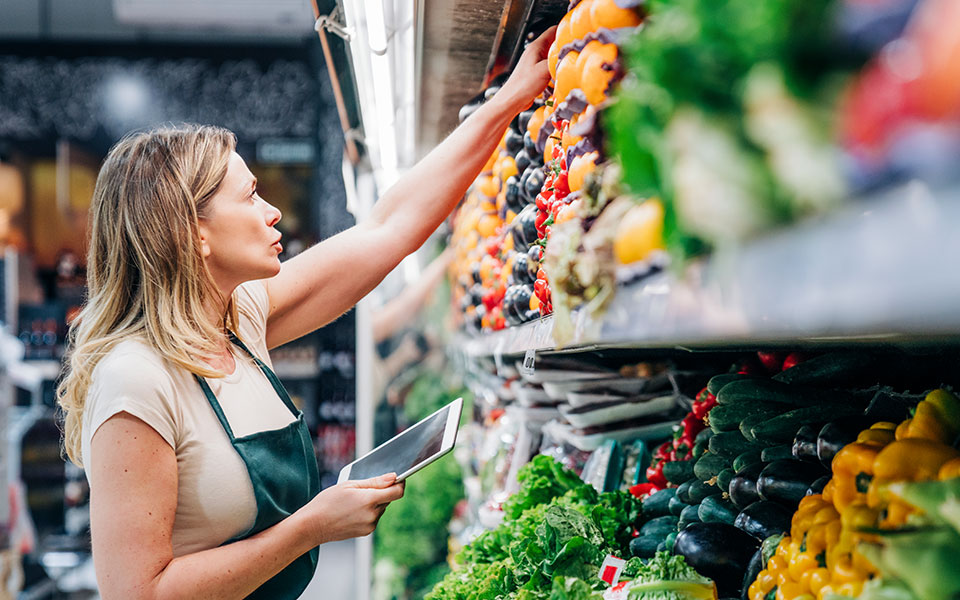
8 proven strategies for rigorous cold chain management
Preparing for the approval and safe use of A2Ls in commercial refrigeration applications...
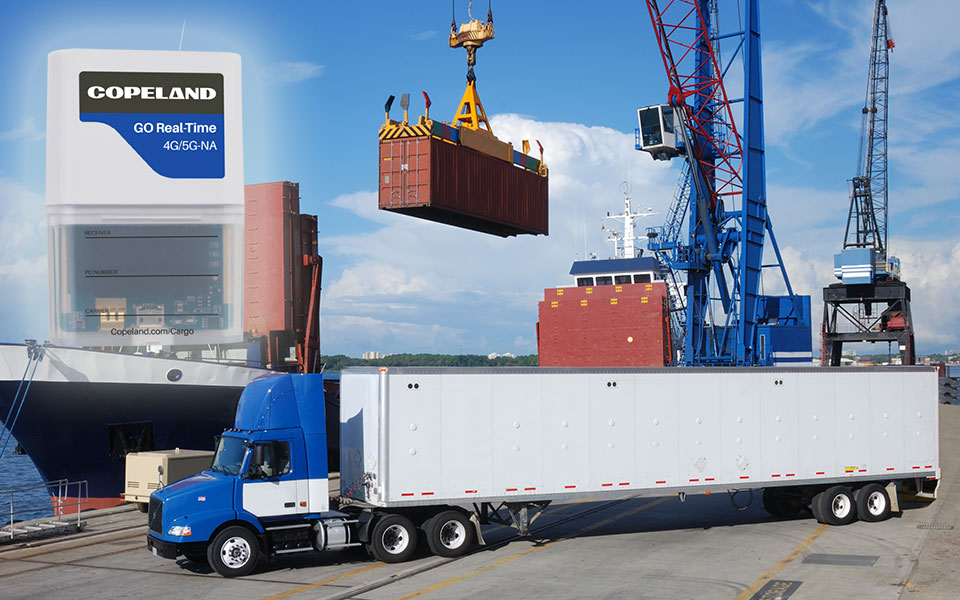
Protection for high-value shipments just got even better
We’re excited to announce the release of Copeland’s newest real-time tracker, the GO Real-Time...
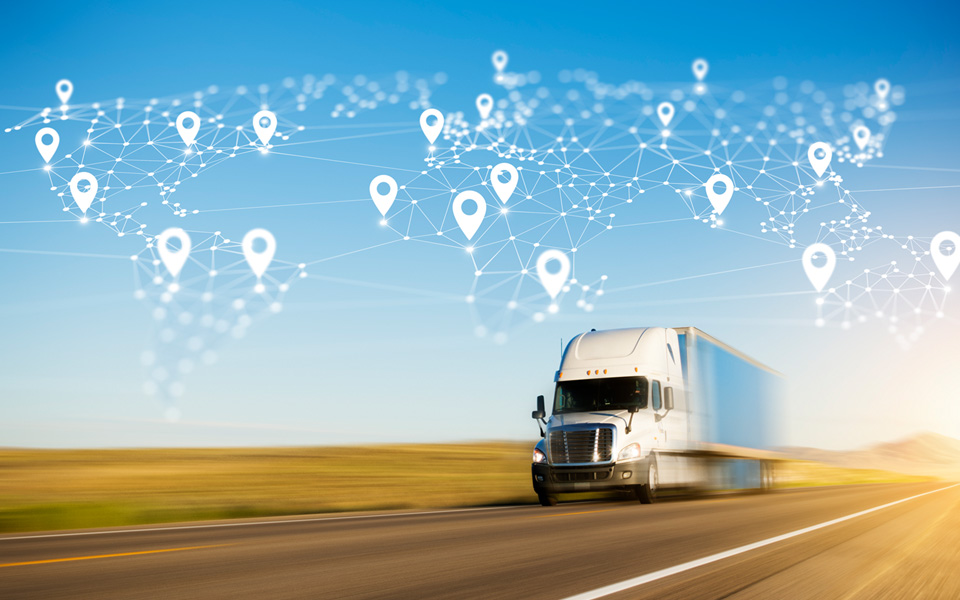
Three proven strategies to prevent cargo theft
The over-the-road (OTR) transport industry is experiencing a surge in cargo thefts. As thieves...